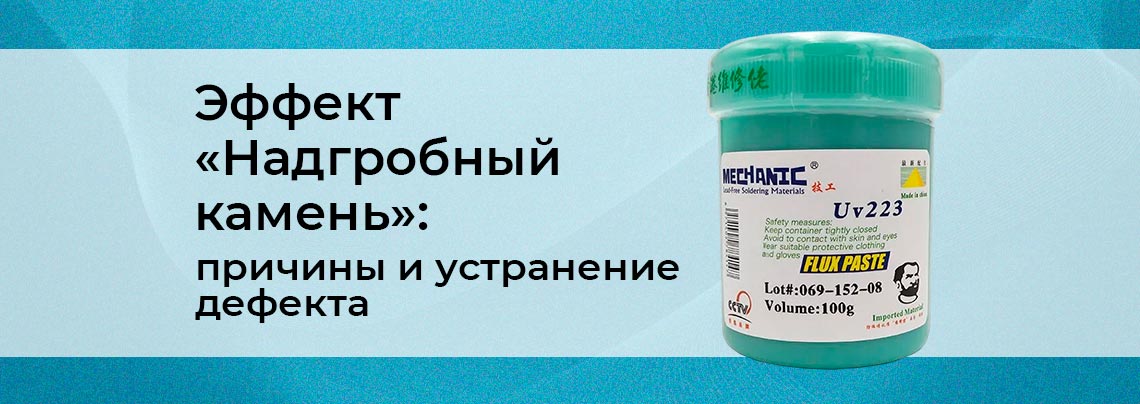
Технология применяющая поверхностный монтаж электронных компонентов родилась еще в 60-х годах прошлого века. Благодаря ее внедрению, компании IBM удалось существенно уменьшить размеры производимых устройств. Это способствовало ее стремительному развитию, а также повсеместному распространению.
Однако миниатюризация компонентов не только уменьшила габариты электронных устройств, но и отразилась на общем качестве производства. Снижение веса элементов, уменьшение толщины платы, а также размещенных на ней дорожек привело к росту образующихся дефектов. Для его устранения потребовались не только новое высокоточное оборудование, но также и разработка новых материалов. В том числе и паяльных составов.
Время чтения: 8 минут
Дефекты при пайке: причины и способы устранения
Дефекты, проявляющиеся при выполнении паяльных работ, вызывают критические нарушения на производстве. Они снижают его эффективность, увеличивают трудовые и временны́е затраты, а также уменьшают общую надёжность конечного продукта.
На этапе пайки может возникнуть множество дефектов: образование перемычек, непропай, затекание припоя, отслоение контактных площадок, разрушение самих элементов, а также множество других.
Для их устранения технологи применяют множество технологических решений от корректировки термопрофиля до совершенствования состава паяльной пасты.
«Надгробный камень»
Наиболее любопытный дефект – это образование «надгробного камня». Дефект проявляется в виде подъёма элемента на ребро, что напоминает надгробную стелу. В некоторых случаях подъем может быть неполным, то есть одна из сторон лишь немного приподнимается, но это не умаляет проблем, возникающих при этом.
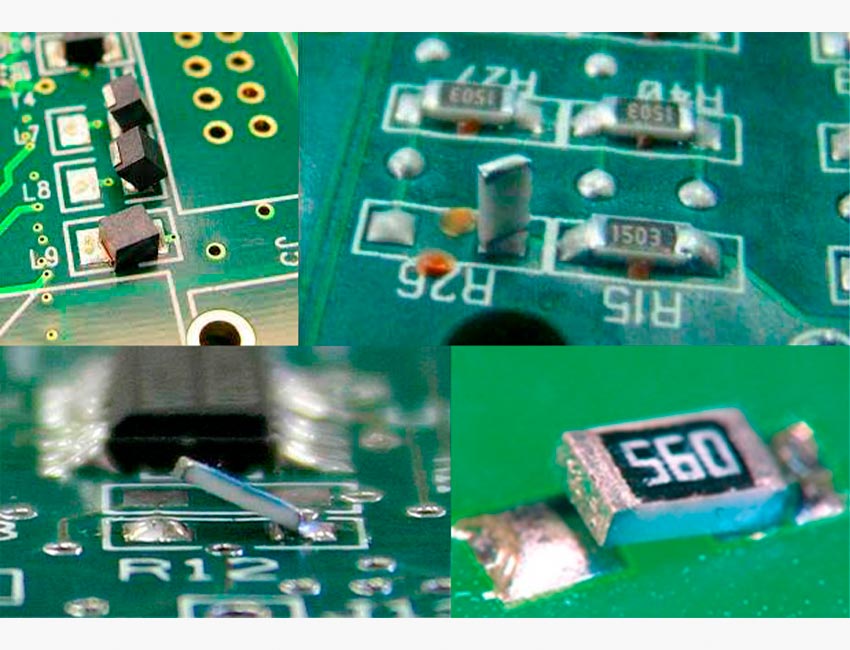
Причины
На проявление эффекта влияют несколько факторов: компоненты и печатная плата, технологический процесс, а также характеристики паяльной пасты.
Влияние компонентов и платы
В качестве основной причины можно выделить плохую паяемость контактов. Неэффективная смачиваемость поверхностей ухудшает прилипание на одной из площадок, что ведет к разрыву соединения.
Другая причина – неверный подбор элементов по размеру. При несоответствии линейных размеров элементов расстоянию между контактными площадками или их размером возникают чрезмерные усилия со стороны припоя. Они могут иметь как продольное, так и скручивающее направление.
Третий фактор – неравномерное распределение тепловой энергии по поверхности печатной платы (PCB, от англ. printed circuit board). Загораживание нагреваемых контактных площадок другими элементами приводит к тому, что припой оплавляется неравномерно. Это приводит к тому, что более оплавленный контакт «перетягивает» электронный компонент на себя.
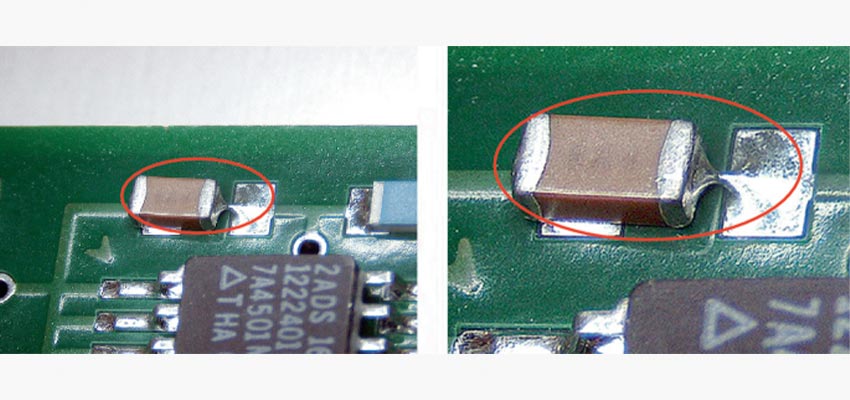
Технологическое влияние
Нарушение технологии пайки – частая причина вызывающая появления самых разнообразных дефектов. Одна из причин – это ошибки при нанесении пасты для трафаретной печати. Это может быть: смещение трафарета, не полный перенос, а также ряд других.
Другая причина – размещение компонентов со смещением. Это явление может возникать из-за отсутствия калибровки SMD установщика, ошибок в ее программе, а также из-за слишком высокой скорости выкладки.
Третья – это неверно подобранный режим нагрева. Зачастую это неверные температурные границы, а также слишком короткое время третьей зоны термопрофиля.
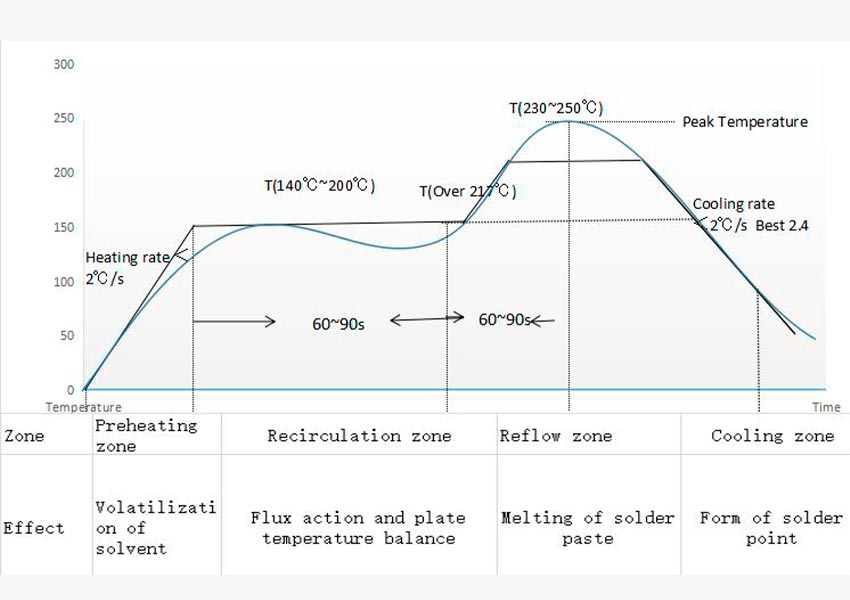
Влияние припоя
Качество, а также физико-химические свойства пасты, используемой в пайке СМД компонентов, оказывает не последнее влияние на образование качественного паяного соединения. Она должна обладать достаточной липкостью, иметь определенную скорость оплавления, а также хорошую смачиваемость. На все эти параметры прямое влияние оказывает ее консистенция.
Паяльные пасты
Ранее повсеместно применялась пайка омыванием контактов расплавом оловянно-свинцового припоя. Однако такая технология сопряжена с риском перегрева платы, что может привести к ее повреждению. К тому же такой способ пайки не подходит для SMT-технологии.
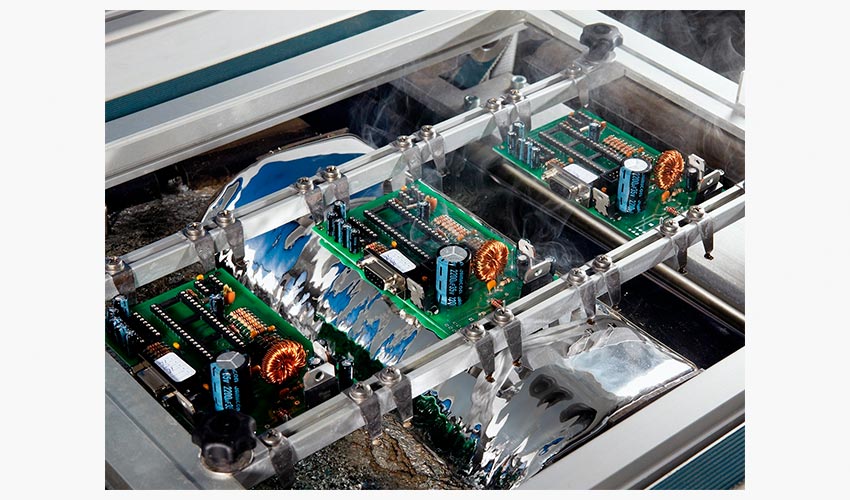
Для этой технологии нужен пластичный низкотемпературный припой, который легко бы наносился на контакты. Изобретение низкотемпературной паяльной пасты позволило существенно ускорить производственные процессы, а также продолжить дальнейшую миниатюризацию компонентов и уменьшить минимальный шаг выводов.
Состав паяльных паст
Все применяемые пасты для лужения приблизительно схожи. Любая паста состоит из двух основных составляющих: небольшого размера частиц припоя, а также флюса. Флюс должен повышать текучесть, способствовать удалению, а также препятствовать дальнейшему образованию окислов.
В состав флюса для пайки включают галогенсодержащии соединения либо органические кислоты. Безгалогенные флюсы относятся к инертным. Минимальное содержание и сниженная активность позволяет им практически полностью расходоваться в процессе пайки. Такие составы называют безотмывочными пастами.
Конечное соединение создается расплавляемыми частицами порошка припоя. При этом важны не только финальная прочность и пластичность соединения, но и его поведение в процессе нагрева, а также такие характеристики, как температуры солидуса и ликвидуса.
На температуру плавления паяльной пасты, а также кристаллизацию влияет концентрация входящих в нее элементов. Эти смеси включают несколько металлов, все они имеют различные точки плавления и кристаллизации. В процессе нагрева происходит поочередное плавление металлов, от менее тугоплавкого к более тугоплавкому.
За температуру ликвидуса (лат. Liquidus – жидкость) принята граница, при которой все металлы входящие в припой переходят в жидкое состояние. В противовес этому показателю – граница полной кристаллизации расплава. Её называют температурой солидуса (лат. Solidus – твердый).
Проблема малого веса
Переход на миниатюрные компоненты 0402, а также 0201 привел к резкому росту образования «надгробных камней». Корректировка термопрофиля не принесла существенных улучшений. Проанализировав поведение элементов, выяснилось, что причина этому – узкий температурный диапазон между ликвидусом и солидусом. Из-за быстрой смены агрегатного состояния не получалось добиться относительно одинакового изменения поверхностного натяжения на всех участках пайки. Как следствие, это приводило к неравномерному распределению механических усилий, создаваемых на концах элемента.
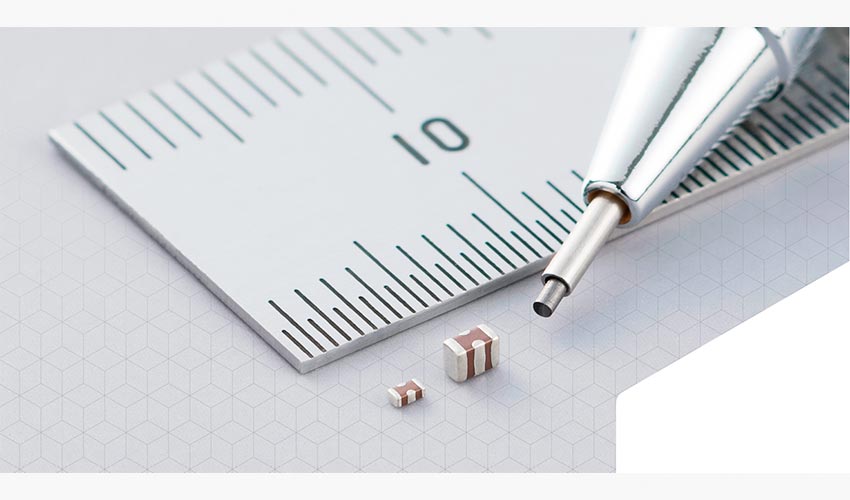
Совершенствование состава
Для расширения температурного окна потребовалась разработка совершенно новой паяльной пасты. Помимо, классически включенных свинца и олова, необходима была добавка, расширяющая границы между полным плавлением и кристаллизацией. Этим исследованием занялись специалисты компании Indium Corp.
В качестве добавки рассматривались такие химические элементы, как висмут (Bi), германий (Ge), индий (In), медь (Cu), серебро (Ag), сурьма (Sb), а также цинк (Zn). В результате проведенных опытных исследований высинилось, что набольший положительный эффект оказало добавление серебра. Дальнейшим стало определение оптимального соотношения, которое оказалось следующим: 0,3…0,4% серебра, 62…64% олова и 36…38% свинца.
В итоге специалистами удалось расширить разницу температур почти до 7 градусов, что уменьшило частоту подъема элементов до 0,3%.
Преимущества модернизированного состава
Помимо, расширения температурного окна ликвидус-солидус паста получила некоторые дополнительные преимущества:
- хорошую смачиваемость поверхностей с высокой окисленностью;
- высокую паяемость контактов;
- хорошую заполняемость апертур в трафарете;
- снижение стоимости, по сравнению с припоями, содержащими 2% серебра.
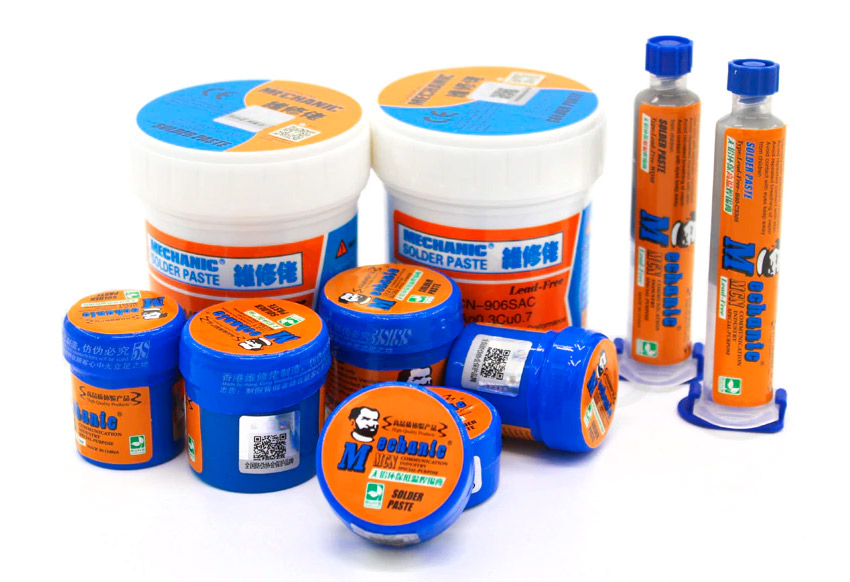
Большое разнообразие паяльных паст позволяет выбрать именно тот состав, который больше всего подходит для решения тех или иных задач. Специалистами разработаны паяльные пасты для использования различных технологических приемов: трафаретная печать, ручное, а также автоматическое машинное нанесения. Также на выбор влияет используемый термопрофиль, а также тип применяемого для оплавления оборудования.
Правильный выбор, а также учет всех технологических особенностей позволит избежать не только проявления эффекта «надгробного камня», но также и многих других дефектов пайки smd компонентов. Это обеспечит высокое качество производства, надежность и конкурентоспособность выпускаемого продукта.