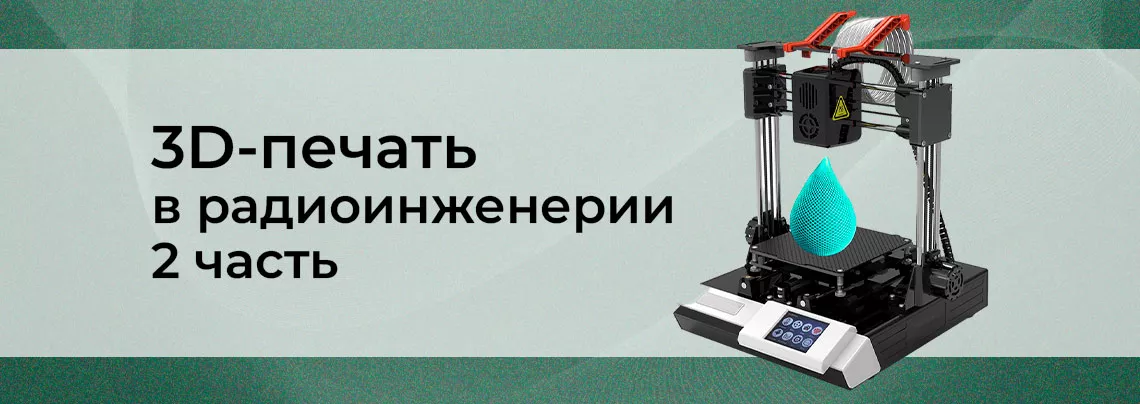
Сейчас доступно несколько разных методов аддитивного (то есть с помощью добавления материала) создания деталей. Это классический, популярнейший в среде непрофессионалов метод послойного наплавления материала (FDM), селективное лазерное спекание порошкового материала (SLS), лазерная стереолитография (SLA), использующая фотополимерную смолу, затвердевающую при засветке лучом лазера, а также другие, имеющие узкоспециализированное назначение. Кроме пластика, современное промышленное оборудование использует металл, керамику, стекло, другие материалы, чтобы печатать детали аддитивным методом.
Ещё стоит упомянуть о «строительных» 3D принтерах для «печати» каркасов зданий из цементного раствора. Но мы с вами, читатели, интересуемся электроникой и робототехникой. Нам скорее интересно, как использовать 3D принтер для получения необходимых конструктивных элементов: корпусов DIY поделок, различных движущихся частей, шестерён, а также разных крепёжных деталей. Как выбрать 3D-оборудование и какое, мы уже разобрались, а теперь, во второй части статьи, поговорим о технологиях 3D-печати.
Первую часть вы можете прочитать здесь.
Время чтения: 22 минуты
Основные методы 3D печати
Ниже рассмотрим базовые широкодоступные методики 3D печати, применяемые в среде профессионалов, а также любителей разработки электронной и робототехники. Сложные методы, применяемые только в промышленности, рассматриваться не будут.
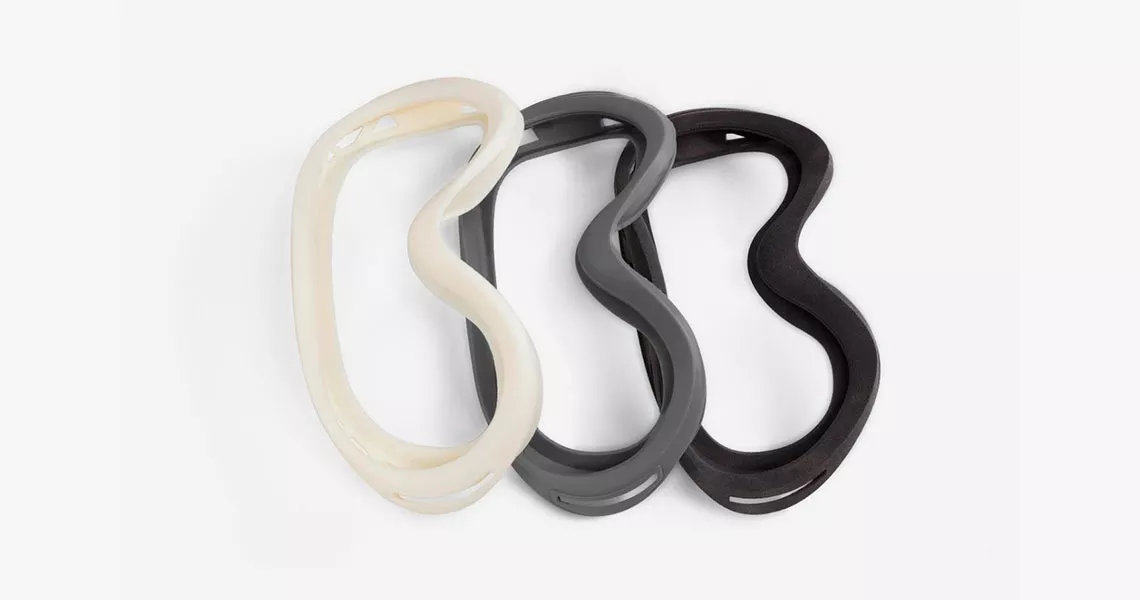
Послойное наплавление материала (FDM)
Метод послойного наплавления материала (Fused Deposition Modeling, FDM) — это самая широкодоступная, массовая технология. Её принцип основан на продавливании термопластичного полимера через нагретое сопло, которое расплавляет полимерный состав, послойно наносит его, формируя так объёмный объект.
Создание 3D-объекта в FDM требует, первоочерёдно, работы с файлом модели формата STL (от англ. StereoLithography, основной формат файла модели для 3D печати), который поддерживают почти все среды, способные создавать 3D модели. Структура формата файлов позволяет через специальное программное обеспечение, называемое слайсер (slicer, от англ. to slice – «нарезать»), правильно разбить модель на слои и сгенерировать плоскую траекторию перемещения печатающей головки 3D принтера на каждом слое с переходами между ними. То есть сформировать управляющую программу на языке Gcode для 3D принтера.
Непосредственно процесс FDM-печати заключается в расплавлении до жидкого состояния полимерной пластиковой нити, подаваемой в сопло печатающей головки принтера, и непосредственно послойном нанесении расплава, мгновенно сплавляющегося с предыдущим слоем и застывающего. Геометрия нанесения слоёв расплава полимерной нити определяется управляющей программой, по которой работает принтер. После полного прохода одного слоя печатающая головка поднимается на некоторое расстояние вверх для печати нового. Процесс повторяется до полной готовности всего объекта.
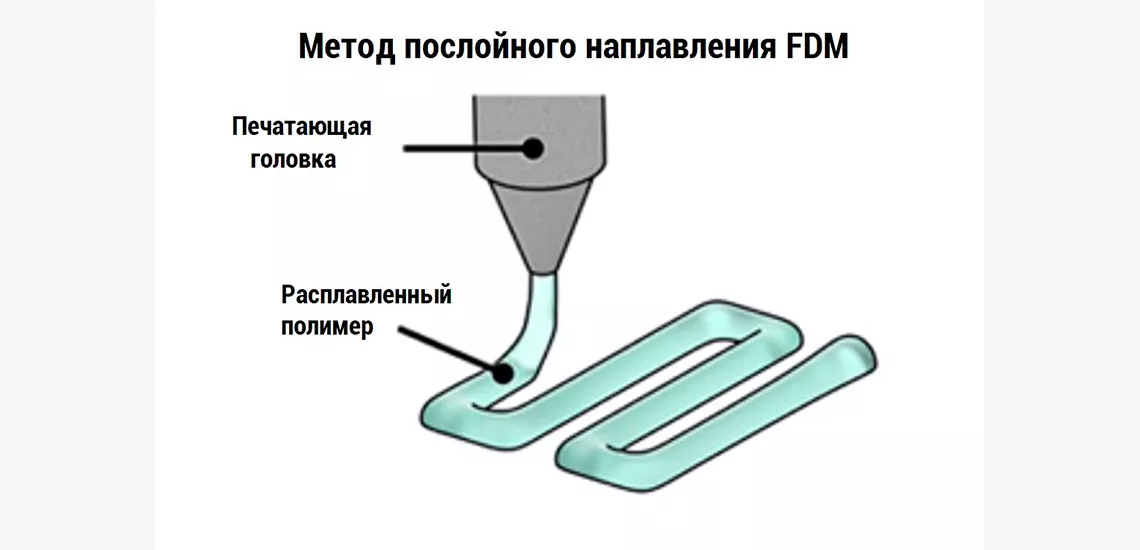
Сегодня придумано немало материалов для FDM-печати. Но чаще остальных используют эти:
- PLA (полимолочная кислота). Жёсткий, хрупкий, совершенно не термостойкий.
- PETG (полиэтилентерефталатгликоль). Более гибкий и прочный, чем PLA, но с множеством нюансов печати.
- ABS (акрилонитрил-бутадиен-стирол). Прочный, но склонный к деформации.
- Nylon (нейлон). Очень прочный, но дорогой.
- TPU (термопластичный полиуретан). Упругий, но гибкий. Требует системы прямой подачи нити в 3D принтере (direct-drive extruder).
Есть более экзотические виды пластика, содержащие внутри себя углеродное волокно, порошковый краситель, древесную пыль, другие наполнители. Их применяют, чтобы улучшить эстетику отпечатанного изделия. Поскольку эта технология имеет хорошие преимущества, FDM часто выбирают в области нефункциональных прототипов при отработке концепции и любых прототипов в целом, производственной оснастки, а также деталей конечного использования. Это часто применяется в небольших мастерских или радиоинженерных и робототехнических лабораториях. Например, FDM подходит для мелкосерийного производства рабочих деталей и прототипов для отработки формы и геометрической увязки с другими частями изделия.
Не считая частное применение, FDM технология встречается в промышленности для печати общемашиностроительных малонагруженных деталей при единичном или мелкосерийном выпуске, а также в медицинской сфере для печати разных биомедицинских изделий: имплантов, протезов и других.
Достоинства и недостатки
У технологии 3D печати видны несколько проблем. Первая связана с её стоимостью. Хотя в целом 3D печать — «дорогое удовольствие», те, кто хочет заняться изготовлением методом послойного наплавления FDM, имеют преимущество с самого начала, так как FDM 3D принтеры — в числе самых дешёвых и доступных, особенно для дома или частных мастерских. Многие модели принтеров сегодня есть в предварительно собранном виде и в виде конструктора для сборки, который ещё дешевле. А выбор моделей попросту огромен!
Ещё одним преимуществом, FDM стало то, что эта технология считается очень чистой, отлично подходит для домашнего или офисного использования. FDM также печатает детали сложной геометрии с внутренними полостями, которые изготовить каким-то другим способом сложно.
Но есть минусы. FDM-печать не достигает того же уровня точности и качества, какой даёт лазерная стереолитографии (SLA). Результат считается удовлетворительно качественным, где бы его потом ни применяли. Разрешающая способность зависит в основном от диаметра выходного отверстия установленного сопла. Точность позиционирования принтера зависит от жёсткости рамы, качества приводов осевых перемещений.
Ещё есть ограничения геометрии печатаемых деталей. Вес верхних слоёв иногда давит на нижние, находящиеся в размягчённом состоянии, так как контактируют с разогретым столом. Это приводит к их деформации (сдавливанию). Ещё учитывают угол между столом и нависающими элементами: если он будет острым, то возможно провисание печатаемых элементов с частичной или полной дефектностью. Иногда требуются поддерживающие конструкции, которые печатаются вместе с основной деталью.
В отличие от SLA, FDM имеет повышенную технологическую сложность. Учитывать нужно вес и размер, а также физические и геометрические ограничения. Даже при большом опыте, скорее всего, потребуется как минимум 1–2 пробных «прогона», перед тем как изготовить «боевую» деталь. Дополнительную сложность вносят «капризные» материалы, требующие тонкого подбора режима печати, особых условий хранения с эксплуатацией.
Ещё одна отрицательная сторона FDM: он в целом медленнее по сравнению с SLA или SLS. А качество поверхности считается лишь удовлетворительным, то есть далеко не на том же уровне, что у упомянутых выше технологий. Фактически при FDM-печати всегда есть вероятность, что деталь потребует постобработки, особенно если важна эстетика.
Селективное лазерное спекание (SLS)
Это метод, который использует лазер в качестве источника энергии для формирования твёрдых 3D объектов. Он был разработан Карлом Декардом, студентом Техасского университета, и его профессором Джо Биманом в 1980-х годах. Позже они участвовали в основании компании Desk Top Manufacturing (DTM) Corp., которая была продана своему крупному конкуренту 3D Systems в 2001 году. SLS в некотором роде очень похож лазерную стереолитографию. Отличие в том, что первый использует порошкообразный материал, а второй — жидкую полимерную смолу. В отличие от SLA или FDM, селективное лазерное спекание не требует использования поддерживающих конструкций при сложной геометрии детали, поэтому сокращается количество расходника.
Технологический процесс SLS-печати относительно несложен. Порошок, загруженный в принтер, распределяется специальным ножом (ракелем) тонким равномерным слоем в области печати, а лишний удаляется в бункер. Лазерный луч высокой интенсивности засвечивает те области, в которых расположены элементы будущей детали: в тех местах, на которые попал лазер, происходит спекание порошка. Затем стол опускается на заданную толщину слоя вниз, а ракель вновь заполняет рабочую область порошком. И так далее, слой за слоем, формируется деталь.
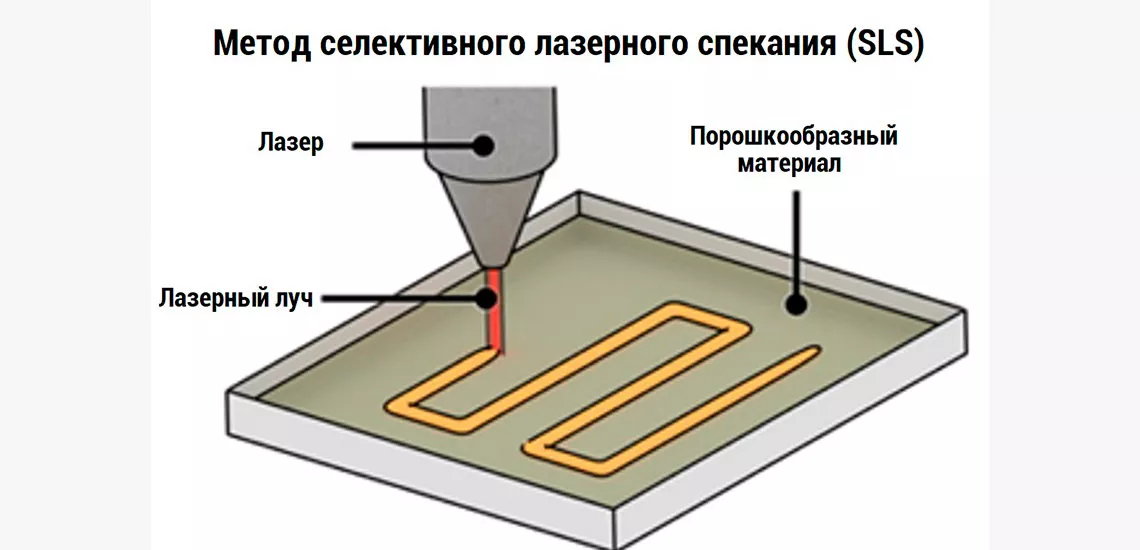
SLS работает на разных материалах: полимерных порошках, металлической пудре, а также различных условно неплавящихся материалах (стекло, керамика) в смеси со связующим веществом. Чаще других встречаются:
- PA (полиамид, он же нейлон). Имеет много разновидностей, но общая черта полиамида — высокая прочность с химической стойкостью. Часто включает разные наполнители, изменяющие физические и химические свойства базового материала: углеродное волокно, стекло, керамика и другие. Чрезвычайно популярен.
- PP (полипропилен). Стойкий к ударным нагрузкам. Популярен и распространён. Имеет отличную спекаемость, склонен к образованию монолитных соединений в местах сплавления.
- TPA (термопластичный полиамид). Более гибкий, чем базовый полиамид. Имеет низкую плотность и вес.
- TPC (термопластичный сополимер). Чрезвычайно гибкий, стойкий к низким температурам.
- TPU (термопластичный полиуретан). Гибкий, стойкий к химическому воздействию.
- PEEK (полиэфирэфиркетон). Обладает высокой термо- и огнестойкостью, жёсткостью, прочностью, способности к стерилизации.
- PEKK (полиэфиркетонкетон). Чрезвычайно прочный, способный в некоторых областях заменить металл. Жаростоек.
Помимо пластиковых порошков, метод SLS применяет металлические порошки алюминия, серебра и даже титана или стали для производства высокопрочных деталей.
Сферы применения SLS обширны: от автомобильного сектора до потребительских товаров. Например, её используют для быстрого прототипирования в разных коммерческих отраслях, выпуска деталей конечного использования малыми партиями. Например, в аэрокосмической промышленности SLS участвует в создании прототипов для компонентов летательных аппаратов. Это представляет большое финансовое преимущество для компаний, поскольку самолёты собирают в небольших количествах, ведь авиакомпании используют их довольно долго. Поэтому для производственных компаний невыгодно создавать металлические шаблоны, плазы и другую оснастку для элементов самолётов. Фактически вся эта оснастка была бы слишком дорога в изготовлении, а большую часть своего жизненного цикла хранилась на складе, притом в идеальных условиях.
Поэтому SLS идеален для небольших партий деталей или оснастки, которую дешевле через несколько месяцев или даже лет напечатать вновь, чем затрачивать средства для хранения долговременных металлоизделий. Ещё интересно, что SLS медленно внедряется в сектор потребительских товаров — например, в создание обуви. По словам производителей, использование нейлона, спечённого методом SLS, позволяет выпускать обувь не только с уменьшенным весом, но и с подгонкой под конкретного заказчика ещё при проектировании.
Успешное применение металлического порошкообразного алюминия и титана в SLS стал одним из примеров огромных будущих возможностей для военной, аэрокосмической, медицинской, других отраслей промышленности, стремящихся использовать малый вес, прочность, коррозионную стойкость титана. Большая часть новаторской деятельности в области 3D печати использовала только пластик, а переход от пластика к прочным металлам становится следующим шагом.
Достоинства и недостатки
Преимущество SLS — оно не требует поддерживающих конструкций, поскольку полностью самоподдерживающее. Поэтому позволяет встраивать одни детали в другие в процессе, называемом вложением: во-первых, это снижает затраты на материал, который, следовательно, мог бы быть израсходован на поддерживающие конструкции, широко используемых в технологии FDM; во-вторых, SLS печатает детали если не любой, то почти любой задаваемой конфигурации. Некоторые настолько сложны, что изготавливаются только селективным лазерным спеканием и более никак.
SLS считается самой быстрой технологией 3D печати для создания функциональных, долговечных прототипов, оснастки и деталей для конечного пользователя. Долговечность конечных продуктов достигается за счёт прочных материалов, таких как полиамид (нейлон), что также даёт определённую свободу в функциональности конечной 3D печати. Кроме того, из-за превосходных механических свойств, материалы, используемые в SLS, часто заменяют типичные литьевые пластмассы.
SLS-методом печатают детали, которые обычно оцениваются как очень прочные и жёсткие, с хорошей химической стойкостью. Сложные изделия с внутренними компонентами, каналами и полостями печатаются практически безо всяких ограничений. Высокая точность — ещё одно весомое преимущество SLS-технологии. Технологический процесс тоже значительно быстрее по сравнению с методом FDM. Но один серьёзных минусов SLS-метода — высокая стоимость оборудования и расходных материалов. Также обычно детали, изготовленные через SLS, имеют определённую пористость поверхности, то есть тоже имеют склонность к необходимости постобработки.
Лазерная стереолитография (SLA)
Это метод изготовления объёмных объектов, использующий лазерный луч для отверждения жидкого полимера. Это старейшая технология 3D печати, но она всё ещё активно используется. Техпроцесс выполняется на специализированном 3D принтере, иначе — стереолитографом, который преобразует жидкий полимер в твёрдые объёмные объекты. Формирование, как и при использовании других методов, осуществляется послойно. После прохода (засветки лазером) каждого слоя, стол с печатаемой деталью либо опускается (прямая стереолитография) на заданную высоту слоя, либо поднимается (обратная стереолитография), чтобы в области печати вновь появился свежий незатвердевший полимер. Процесс повторяется до полного прохода всех слоёв.
SLA, хоть принципиально схожа с селективным лазерным спеканием, но технологически это разные методы. К примеру, лазерная стереолитография имеет более жёсткие ограничения на геометрию деталей, схожие с ограничениями метода послойного спекания (FDM). И как в FDM, в SLA тоже используются поддерживающие конструкции, позволяющие напечатать «висящие в воздухе» элементы. Другими словами, он требует более грамотной технологической подготовки печати, в отличие от SLS.
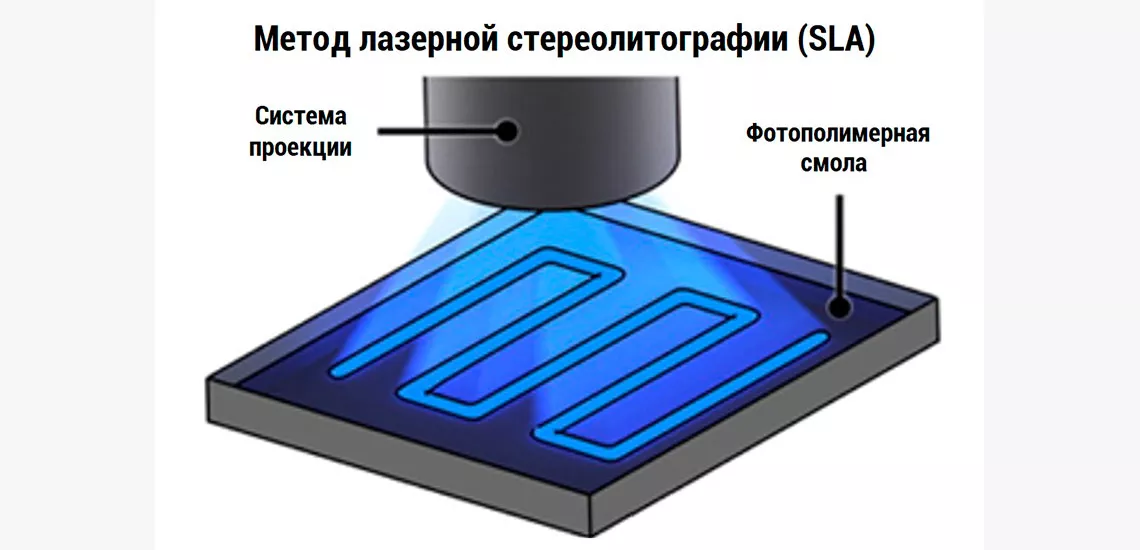
SLA применяет несколько разновидностей полимерных смол, отличающихся химическими и физическими качествами. Точный состав смол — коммерческая тайна производителей, поэтому их условно разделяют по применимости в различных сферах. Наиболее часто употребимыми являются следующие разновидности:
- Базовые смолы. Из них изготавливают предметы быта, декоративные изделия, корпусы электронных приборов и другие конструктивные элементы в радиоинженерии и робототехнике. Не очень прочны и долговечны, но просты в применении и относительно дешевы.
- Инженерные смолы. Являются более прочными, ударо- и химически стойкими, чем базовые смолы. Применяются для изготовления функциональных объектов. Для примерного понимания свойств конкретной смолы в её названии указывают полимер, к свойствам которого тяготеет эта смола (к примеру, nylon-like, abs-like, pp-like и так далее).
- Выжигаемые смолы. Эта разновидность полимерных смол подходит для выплавляемых моделей при использовании в литье металла. Легко тают, освобождая место для жидкого металла.
- Медицинские смолы. Как ясно из названия, они применяются для использования в медицине и служит базой для изготовления имплантов, капп, протезов и аналогичных изделий медицинского назначения. Особенность смол — химическая инертность и возможность длительного контакта с человеком.
Метод лазерной стереолитографии широко применим. Его использует автомобильная, аэрокосмическая, медицинская и потребительская сферы. Фактически его применяют и в бытовой сфере, так как SLA 3D принтеры хоть и недешевы, но относительно доступны. Также эта технология позволяет печатать очень реалистичные модели анатомических частей тела человека, элементов живой природы, скульптур и разных изделий, чтобы задействовать объекты, напечатанные SLA-методом, в образовательной деятельности.
Достоинства и недостатки
Среди всех технологий 3D печати SLA — одна из лучших; в основном её «сила» заключается в высокой разрешающей способности. Метод позволяет печатать объекты с очень сложной геометрией. Геометрическая точность даже в «тяжёлом» случае, как правило, оценивается как очень хорошая. «Вторым именем» SLA стала «точность»: метод часто используется там, где форма и точная геометрическая увязка критически важны. Фотополимерные смолы также предоставляют определённую свободу в отношении цветов, фактора непрозрачности и жёсткости, совмещая это при всём с превосходным качеством поверхности.
Хотя есть более быстрые и современные технологии, SLA-метод позволяет печатать детали в разумные сроки. Таким образом, он идеален для производства прототипов, на 100% внешне похожих на оригинал и точностью, на 100% соответствующей точности образца при любой её геометрической сложности. Более того, положительная сторона использования SLA-метода в общем и фотополимерных смол в частности, — многообразие как цветов, так и других эстетических параметров изготавливаемых таким методом объектов. Смолы (и изготовленные из них детали, конечно же) имеют разную степень как прозрачности, так глянцевости поверхности.
Однако высокая стоимость оборудования и расходников — один из основных недостатков. 3D принтеры встречаются более или менее доступными, но фотополимерные расходники бывают очень дорогими, что делает обычное массовое использование этой технологии для печати всякого ширпотреба типа «подставок для телефона» крайне нецелесообразным. Кроме того, смолы хоть бывают разных цветов, но выбор всё ещё весьма скудный и совсем не сравнится с широчайшей номенклатурой цветов и фактур пластиков для FDM.
Минус SLA, точнее, используемых материалов — что жидкие смолы, как правило, обладают раздражительным действием или вовсе токсичны. Поэтому требуют соблюдения некоторых мер предосторожности при работе с ними. Кроме того, готовые детали обычно требуют очистки от жидкой смолы, что часто долго и сложно. Постобработка, как правило, необходима, если хотите достичь максимального качества. Необходимость финишной обработки также зависит от того, какой материал выбран. А ещё лазерная стереолитография, в отличие от схожего метода селективного лазерного спекания (SLS), требует применения поддерживающих конструкций, что приводит к повышенному расходу «бесценной» смолы, повышая затраты на печать.
Особенности материалов
В FDM в качестве расходника применяется нить из полимера диаметром 1.75 и 2.85 миллиметра. Менее производительные принтеры используют нить меньшего диаметра, а более производительные — большего. Дорогие принтеры, как правило, поддерживают оба возможных диаметра нити. Нить изготавливается из определённого числа различных полимеров с разными свойствами и требованиями к режиму печати. Вот некоторые из самых популярных:
- PLA (полимолочная кислота). Как было сказано ранее, — это жёсткий, хрупкий, относительно дорогой, но полностью экологически безопасный полимер. Им легко печатать, так как он не «капризен», плавится при относительно низкой температуре, не образует нитей, не коробится. В общем-то, одни плюсы, не считая главного минуса: эксплуатировать изделия из этого пластика нельзя при температуре выше 50°C. Другими словами, он способен размягчиться или расплавиться даже жарким летним днём.
- PETG (полиэтилентерефталатгликоль). Самый распространённый вид 3D-пластика, так как поддерживается всеми принтерами. Пригоден для печати практически всего на свете. Более гибкий и прочный, чем PLA, но требует больших усилий в подборе режима. Имеет хорошую адгезию слоёв между собой.
- ABS (акрилонитрил-бутадиен-стирол). Один из самых прочных пластиков, применяемых в 3D печати. Капризен, требует особых режимов и вытяжной вентиляции. Склонен к деформации, короблению. Подходит не для всех принтеров, так как требует высокой температуры плавления.
- TPU (термопластичный полиуретан). Гибкий, маслобензостойкий пластик. Применяется для печати гибких объектов. Требует особых режимов и подбора сопла печатающей головки, так как непрерывная подача такого пластика через сопла малых диаметров практически невозможна. Также применение такого пластика требует от принтера наличия прямого привода подачи нити (direct-drive extruder — нить протягивается приводом, встроенным в печатающую головку).
- Nylon (нейлон). Очень прочный. Применяется для печати высоконагруженных деталей, к примеру, шестерней. Относительно дорогой. Как и TPU, печать этим видом пластика рекомендуется на принтерах с высокомощными нагревателями и высоким температурным режимом.
- PC (поликарбонат). Этот пластик удивительно высокопрочен. Почти прозрачен, пригоден даже для изготовления пуленепробиваемых стёкол и других высокопрочных элементов. Имеет сверхвысокую температуру печати (более 300°C) и требует тщательной настройки режимов. Печать поликарбонатом дома не рекомендуется, ввиду того, что этот пластик в расплавленном виде — источник токсичных испарений.
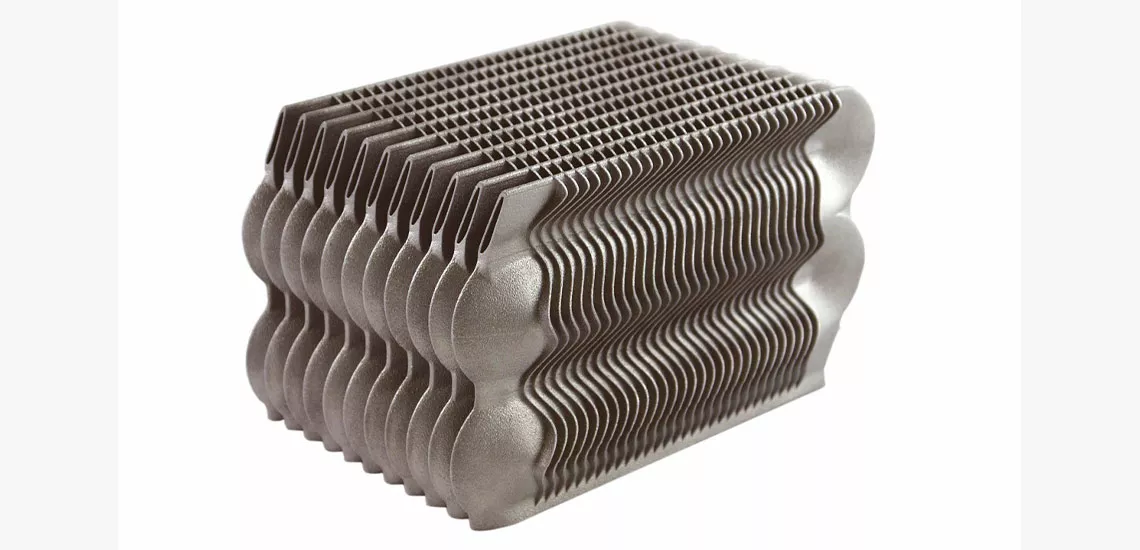
Из всех материалов в SLS популярней всех полиамидные порошки. Чаще всего — нейлон. Он отлично подходит для печати таким методом; этот материал, по сути, жёсткий, прочный, но он также имеет некоторую степень изгибания под высокими нагрузками. Полиамиды также в числе самых дешёвых 3D-расходников.
Постобработка отпечатанных из полиамида деталей включает любые виды полировки, окраски или лакирования, и, следовательно, даёт большую свободу в формировании окончательного внешнего вида готовых изделий. Отрицательной стороной полиамидов стала их гигроскопичность, то есть они быстро впитывают влагу и требуют особых условий хранения.
В SLA базовым материалом выступают различные комбинированные синтетические фотополимерные смолы. Производители выпускают немало смол, которые состоят из различных базовых и присадочных компонентов: комбинаций длинных и коротких мономеров, олигомеров, фотоинициаторов и добавок. Многообразие составов даёт свободу для создания различных составов с богатым набором оптических, механических и термических свойств: от прозрачных до непрозрачных и цветных, от гибких до ультражёстких, от податливых до жаростойких и так далее.
Точный состав смолы — коммерческая тайна производителя и хранится в секрете. Смолы поставляются в виде жидких фотополимеров, которые отверждаются и затвердевают под воздействием ультрафиолетового лазера стереолитографа. Смолы сегодня — в числе лучших материалов с точки зрения возможностей. Технологии, которые базировались на фотополимерных смолах, печатают высококачественные изделия, что делает их выбором для профессиональных сфер, изготовления сложнейшей подготовки «идеальных» макетов и других ответственных деталей.
Преимущества смол — пригодность для печати с высоким разрешением, малая шероховатость текстуры внешней поверхности и отсутствие нужды в её постобработке, множество цветов и свойств, включая прозрачность и полупрозрачность. Недостаток в том, что смолы вызывают местное раздражающее при контакте с кожей, а также имеют токсичные испарения, что обязывает соблюдать меры предосторожности. Хотя материал предлагает большую свободу геометрии деталей, их печать требует поддерживающих конструкций, что увеличивает расход и, следовательно, затраты. Но при выполнении «идеальной» печати, для которой и придуман SLA, стоимость обычно имеет второстепенное значение.
Сегодня вы узнали о наиболее доступных и популярных методах и материалах для 3D-печати, необходимых в техническом творчестве как инженеров-любителей, так и профессионалов. А ведь печать корпусных элементов, ручек, рычагов, тяг и других элементов вызывало наибольшую сложность. Трёхмерная печать увеличила скорость создания техники, которая будет окружать нас и облегчать труд.