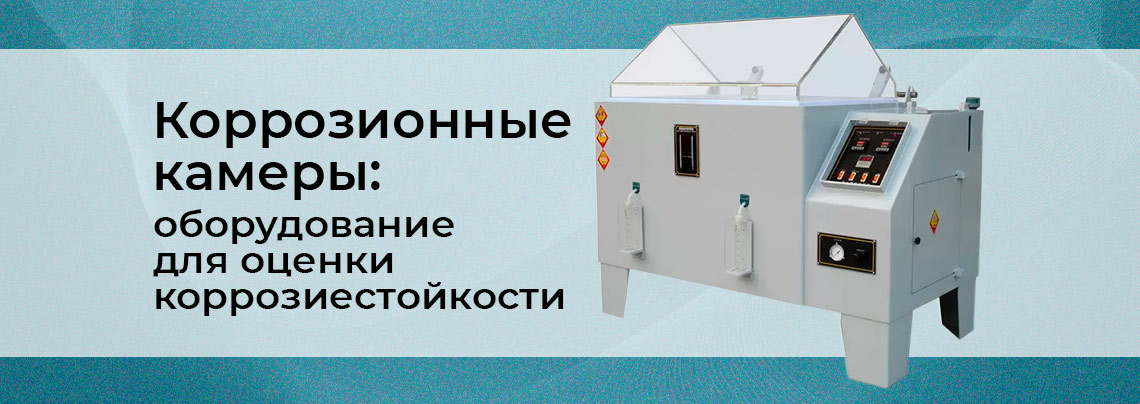
Коррозия — это естественный процесс разрушения веществ под воздействием окружающей среды. Прежде всего, атмосферных факторов. Она наносит весомый ущерб различным отраслям, включая строительство, транспорт, электронику и энергетику.
Время чтения: 30 минут
- Коррозия и её экономические последствия: масштабы, прямые и косвенные потери
- Главные этапы развития науки об окислении металлов
- Что такое коррозионные камеры и зачем они нужны?
- Основные виды окислительных тестов
- Главные параметры выбора профессиональной коррозионной камеры
- Обзор профессиональных камер для испытания на коррозию оборудования из каталога «Суперайс»
Коррозия и её экономические последствия: масштабы, прямые и косвенные потери
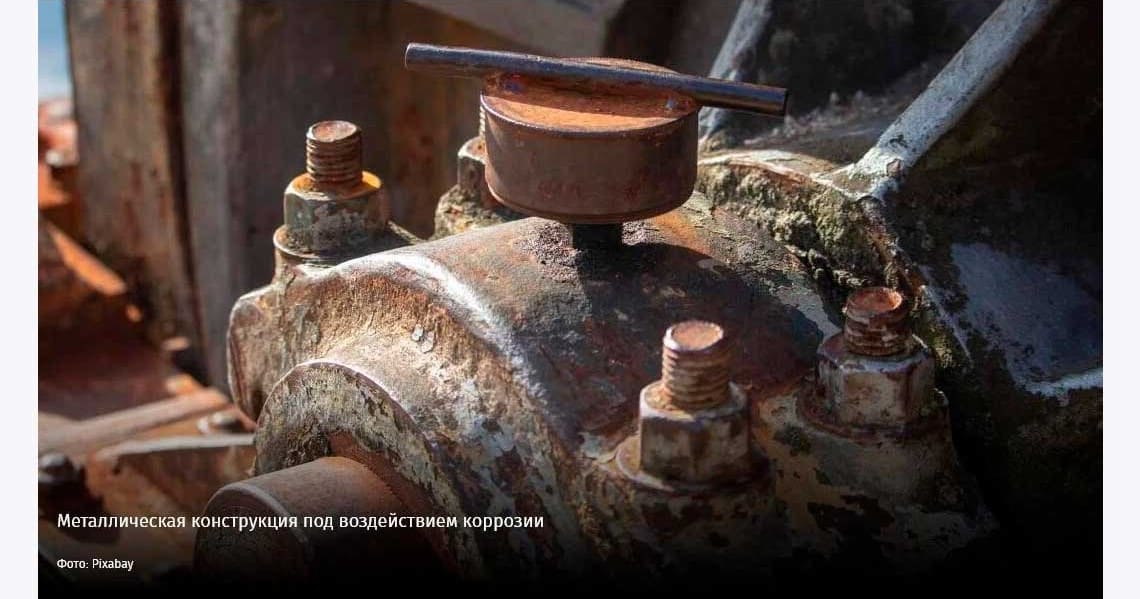
Для борьбы с корродированием в США в 1943 году создали Национальную ассоциацию инженеров-коррозионистов — NACE (National Association of Corrosion Engineers). Эта организация разрабатывает нормативную документацию для аттестации и тестирований материалов нефтегазовой, добывающей и перерабатывающей отраслей промышленности.
По её утверждению, ежегодные потери от окислительной деградации металлов в США достигают 4% от ВВП (валового внутреннего продукта). NACE за 2001 год по отраслям была даже составлена диаграмма «потерь».
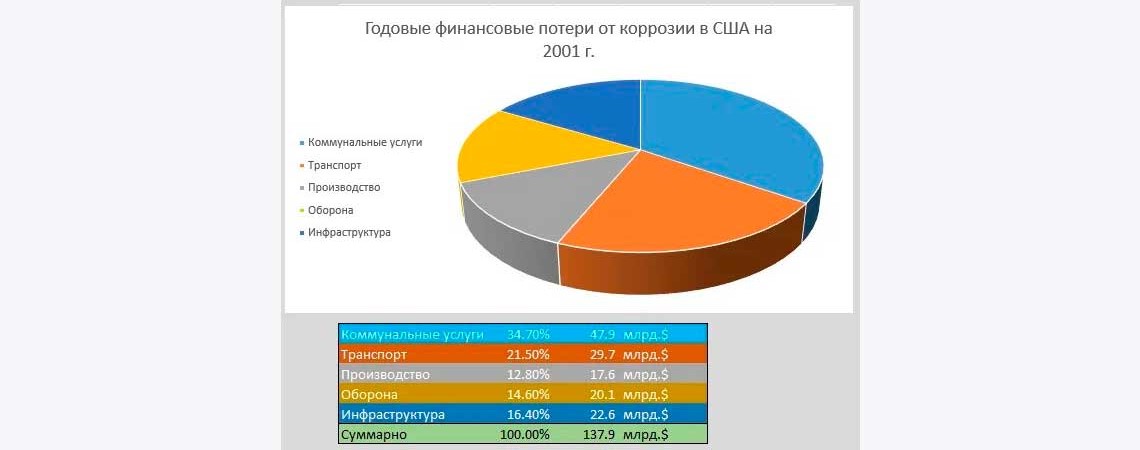
В странах с развитой промышленностью потери составляют от 2 до 4% валового национального продукта. Среди «лидеров» Ассоциация выделяет Индию (4% ВВП) и Китай (3,3% ВВП). А вот Япония, несмотря на влажный островной климат, теряет всего около 1% от ВВП. Знаменитый материаловед России, академик РАН, директор Всероссийского научно-исследовательского института авиационных материалов (ВИАМ) Евгений Каблов в интервью корреспонденту газеты «Известия» Анне Урманцевой объясняет этот феномен тем, что японские учёные внимательнее своих зарубежных коллег отнеслись к проблеме, и за 58 лет научно-исследовательской работы создали национальную систему защиты от коррозии.
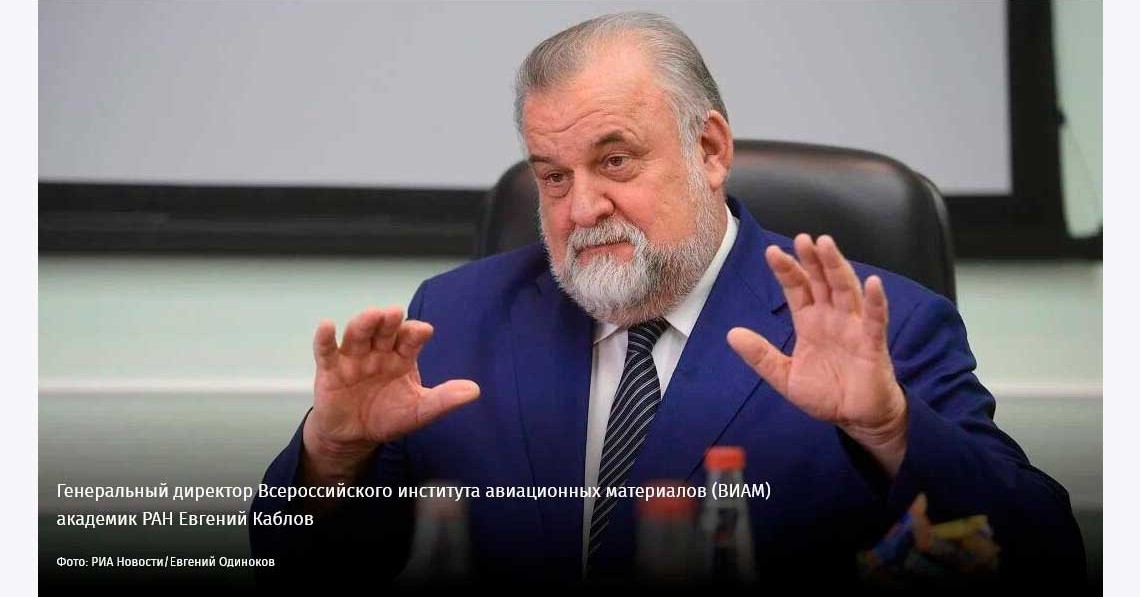
Потери от оксидной деградации бывают прямыми и косвенными.
Прямые:
- цена разрушенной части металла;
- цена вышедшего из строя из-за деградации оборудования;
- дополнительные траты на припуски из-за деструктивного действия ржавления;
- затраты на защитные покрытия и др.
Косвенные:
- простои при повреждении установки из-за окислительного износа;
- убыль или порча окислённой продукции;
- потери, связанные с изменением свойств вещества из-за ржавления (значения теплопроводности, электропроводности и т. п.);
- убыль сырья при разгерметизации машины из-за ржавления;
- снижение пропускной способности трубопроводов из-за деградационных отложений;
- загрязнение продукции ржавчиной.
Потери металла, которые можно повторно использовать, называются ВОЗВРАТНЫМИ. Мелкодисперсные формы отходов, непригодные к утилизации, относят к НЕВОЗВРАТНЫМ потерям.
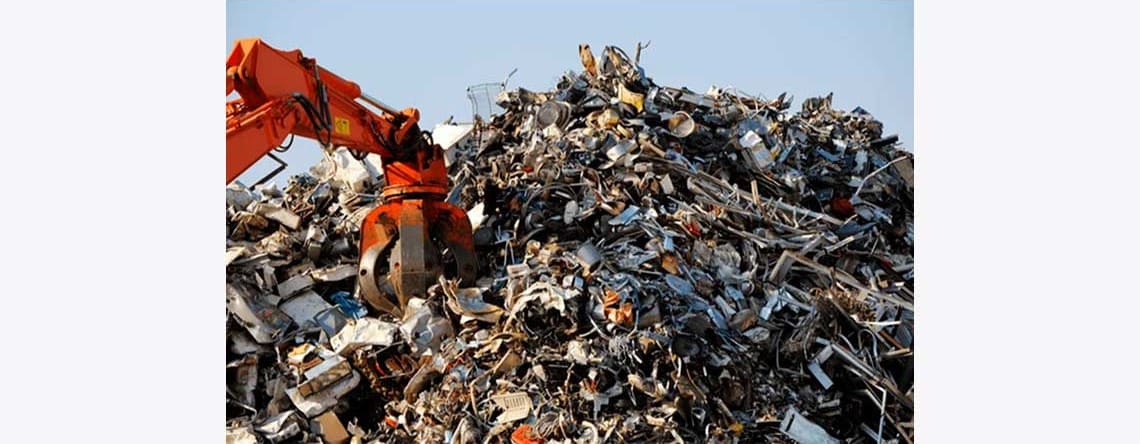
Последствия коррозии
Коррозия бывает причиной аварий и катастроф:
-
США, 1967 год, Серебряный мост. Неправильный выбор материала для конструкции моста и недостаточная защита от разъедания ржой привели к его обрушению, унеся жизни 46 человек.
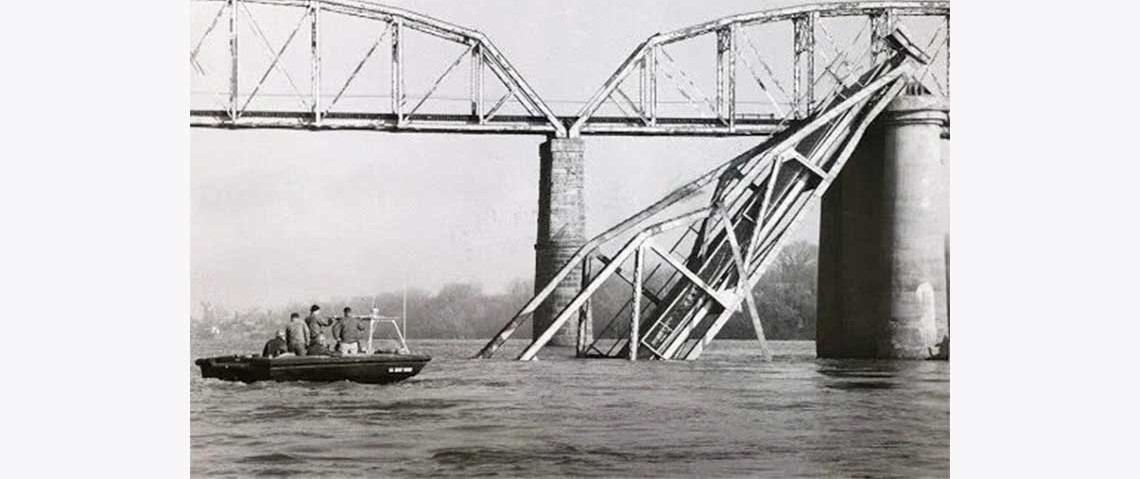
-
США, 1984 год, Мост Гринвич. Проржавело крепление подъёмного механизма. Погибли три человека.
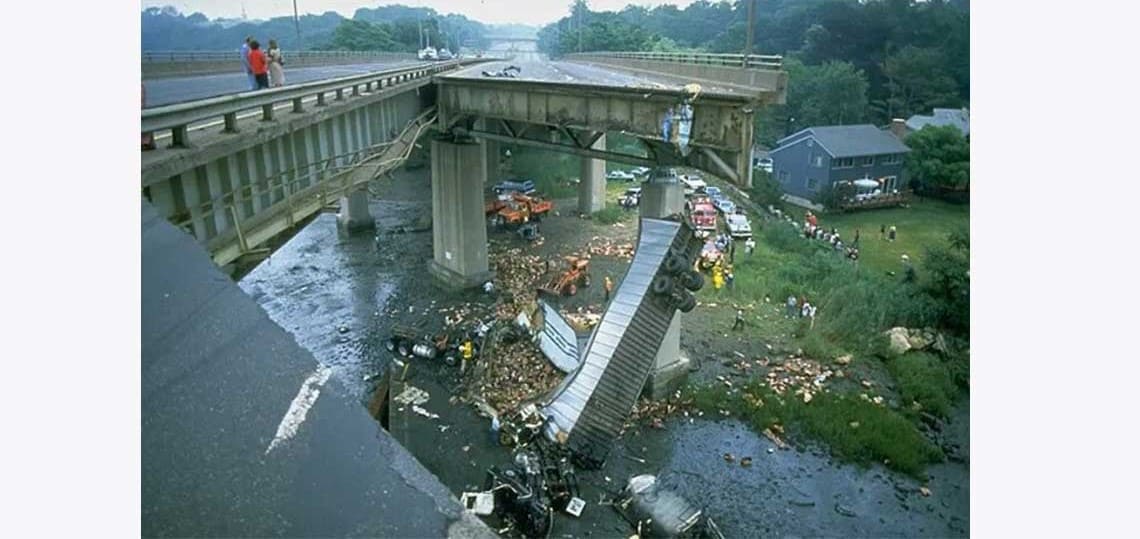
-
Уфимский нефтеперерабатывающий завод, 1991 год. Надлом дымовой трубы над взрывоопасным производством из-за разъедания арматуры привёл к дорогим восстановительным работам.
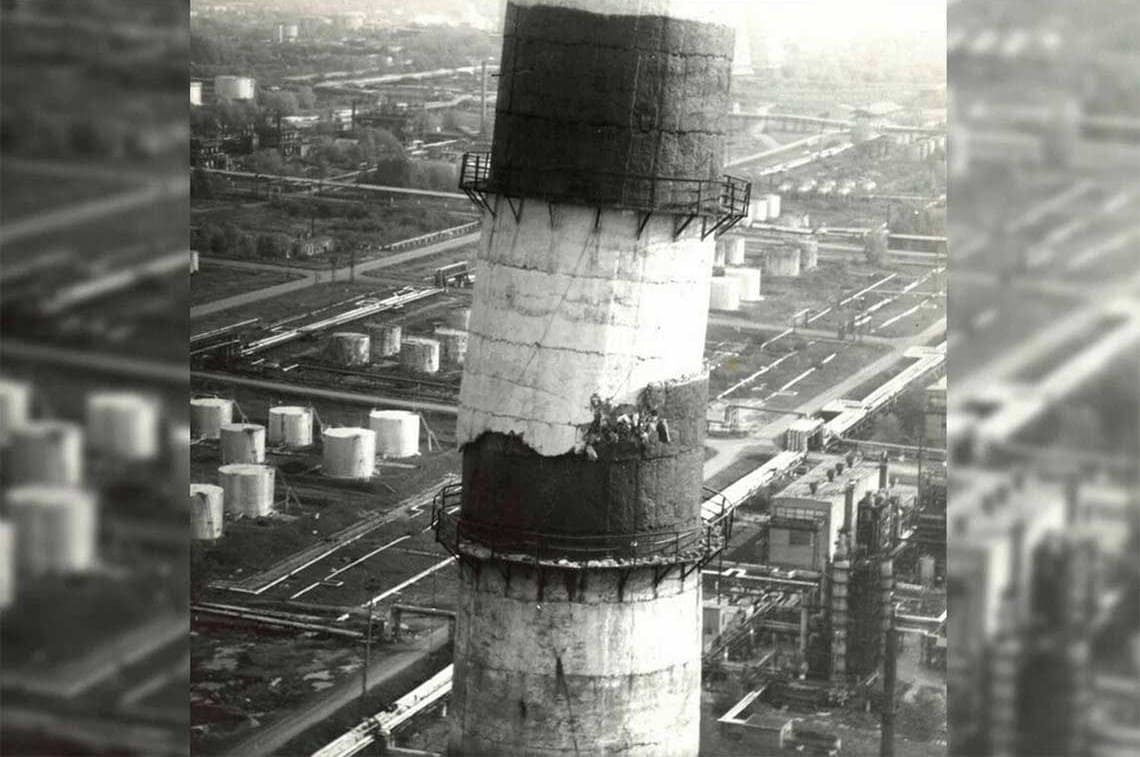
-
Усинск, Республика Коми, 1994 год. Глобальная катастрофа, вошедшая в Книгу рекордов Гиннеса. Проржавевший трубопровод лопнул в нескольких местах. Сотни тысяч тонн нефти залили громадные территории, загрязнили реки и дошли до Баренцева моря. Для её ликвидации потребовался кредит в 124 млн долларов и 15 лет восстановительных работ.
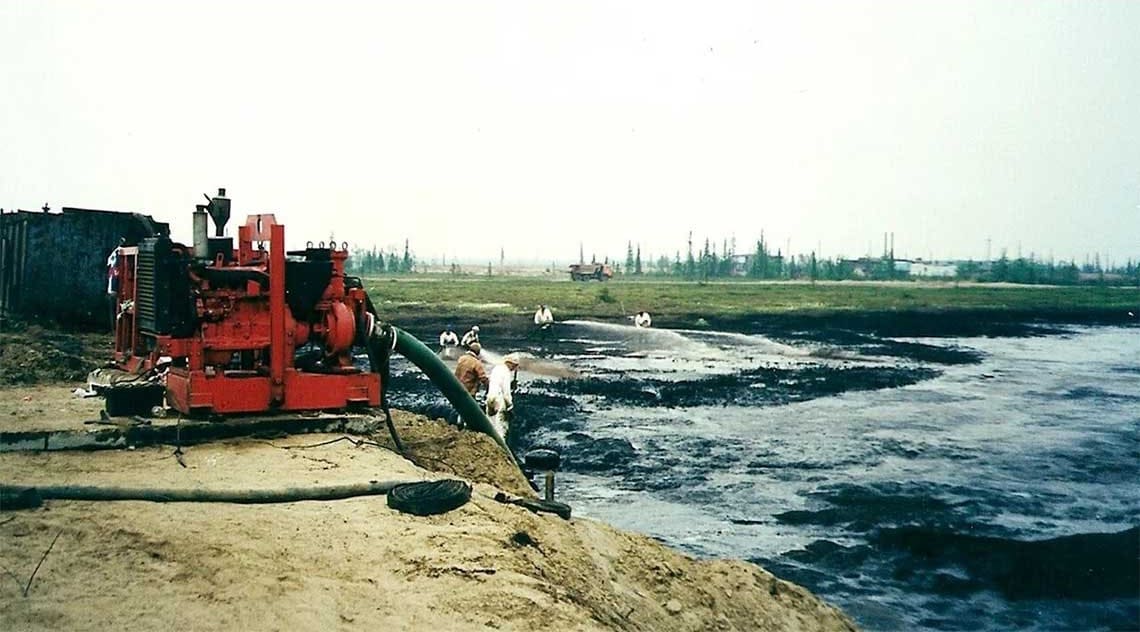
-
Черкесск, 1997 год. Катастрофа самолёта Ан-24 в результате разрушения фюзеляжа из-за оксидной деструкции. Погибли 50 человек.
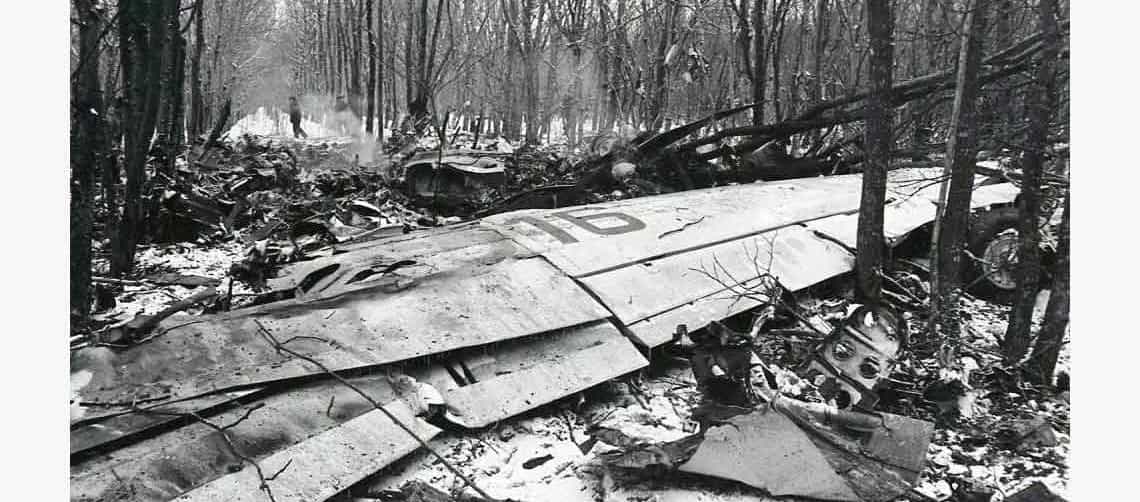
-
Чусов Пермского края, 2005 год. Обрушение крыши бассейна «Дельфин» в результате ржавления балок, где 14 человек погибли, ещё 12 пострадало.
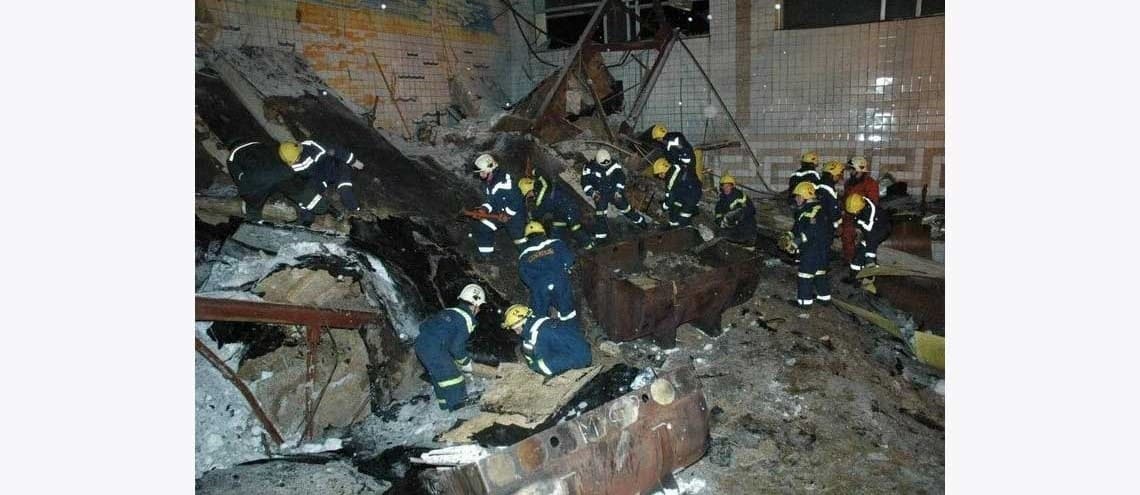
-
Басманный рынок в Москве, 2006 год. Обрушение, вызванное деградацией крепёжных тросов, удерживающих крышу. Погибли 68 человек.
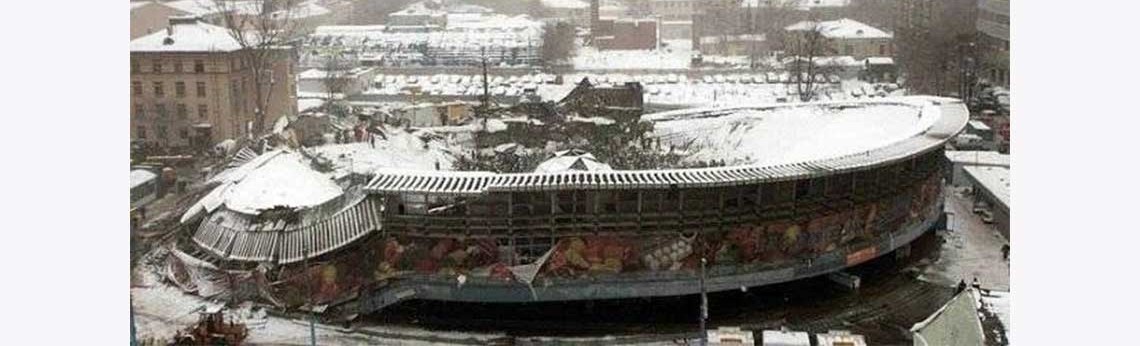
Главные этапы развития науки об окислении металлов
Проблема коррозионного разрушения металлов существует уже несколько тысячелетий, и её изучение прошло через несколько ключевых этапов.
Ранние методы защиты металлов от оксидной деструкции
Появление первых железных изделий около 4–5 тыс. лет назад породило проблему их ржавления. Самым ранним способом защиты металлов от коррозии стали специальные покрытия. Например, в древнем Египте применяли разные смолы, а в древней Иудее обволакивали асфальтом железные конструкции дворца царя Соломона. Римский философ Плиний Старший (23–79 гг. н. э.) описывал разные покрытия для железа, включая свинцовые белила и дёготь.
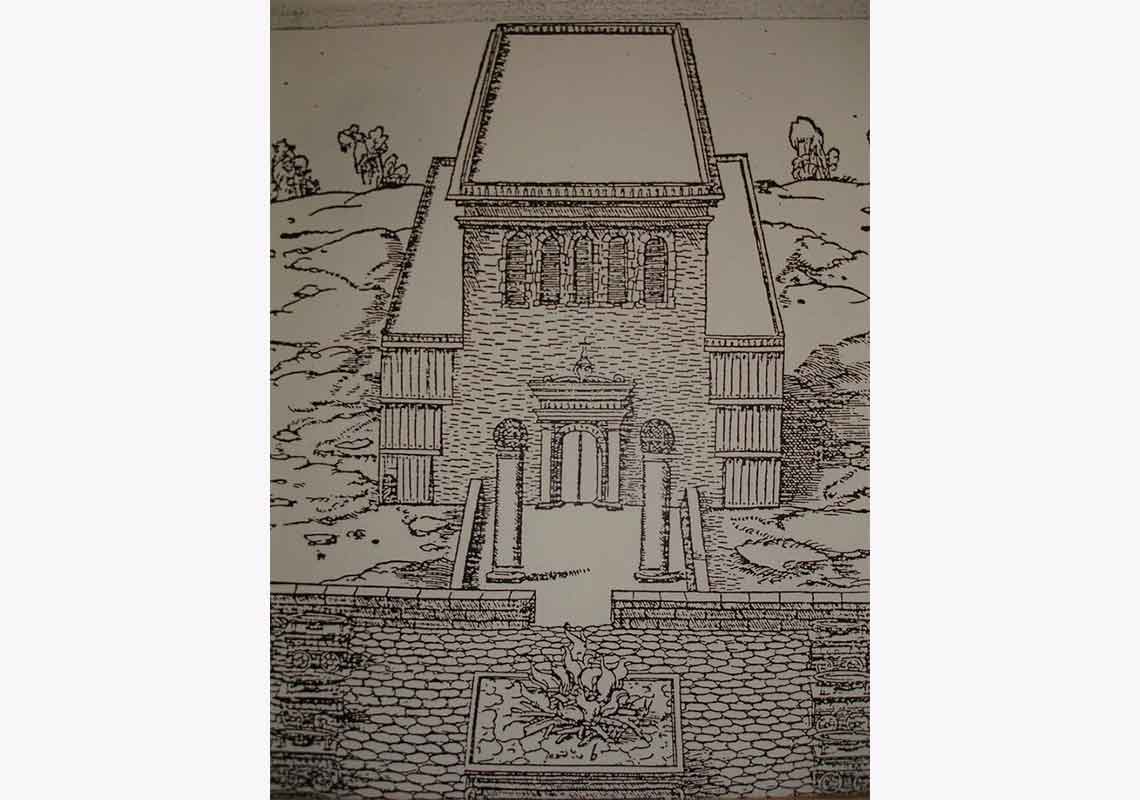
Время | Способ защиты | Место |
950 год. до н. э. | Асфальт | Дворец Соломона |
Древний Египет | Природные смолы | Египет |
I век н. э. | Свинцовые белила и дёготь | Рим |
Научные открытия XVIII—XIX веков
Серьёзные научные исследования оксидного износа начались в XVIII веке. В 1748 году Михаил Ломоносов открыл закон сохранения массы, проведя эксперименты с металлами, подвергавшимися прокаливанию в запаянных сосудах. Его работы опровергли теорию о флогистоне и заложили основы для научного изучения оксидной металлодеструкции. В 1782 году Антуан Лавуазье исследовал окисление железа, показав, что при этом образуются соединения с кислородом. В XIX веке М. Фарадей установил законы электролиза, что стало основой для понимания электрохимического механизма разъедания металлов. Русский учёный Н. Н. Бекетов в 1865 году защитил докторскую диссертацию на тему «Исследования над явлениями вытеснения одних элементов другими».
Год | Учёный | Открытие |
1748 | М. В. Ломоносов | Закон сохранения массы |
1782 | А. Лавуазье | Окисление железа |
1812 | Х. Деви | Выдвинул гипотезу о предотвращении окисления металлов при помощи негативного заряда |
1833–1834 | М. Фарадей | Законы электролиза |
1865 | Н. Н. Бекетов | Явления вытеснения металлов |
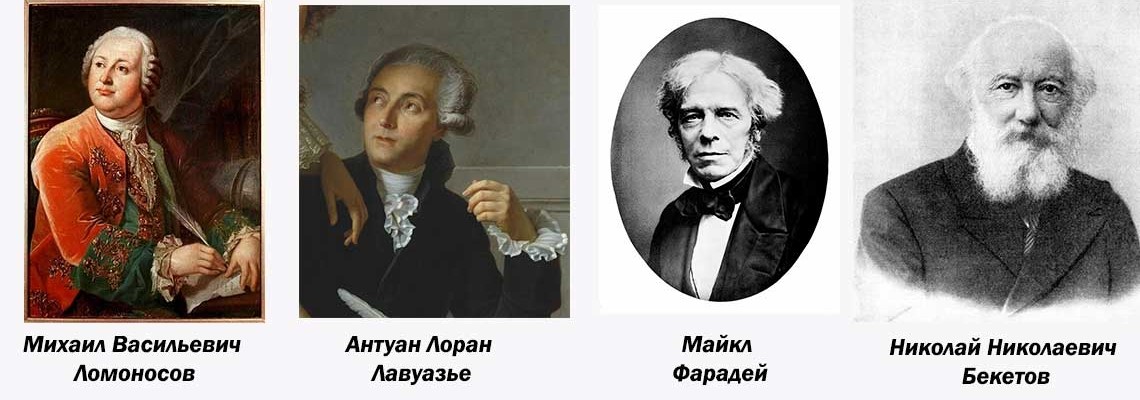
XX век и современное понимание
К 1925 году Гадфилд впервые оценил масштаб потерь от окислительной порчи металлов, подсчитав, что с 1860 по 1920 год было разрушено 660 млн тонн стали. Это осознание послужило основой для строительства специализированных лабораторий для изучения окисления металлов. Первая из таких была основана Г. В. Акимовым в 1929 году.
Работы, проведённые академиком В. А. Кистяковским, стали основой для фильмовой теории коррозии, где пристальное внимание уделялось окисным плёнкам на поверхности металла. Кистяковский открыл мото-химические и мото-электрические явления, связанные с изменением электрохимических потенциалов.
В 1962 году в СССР вышла книга Ю. Р. Эванса «Коррозия и окисление металлов», в которой автор, знаменитый учёный в области оксидной деградации веществ, обобщает результаты научных исследований английской школы коррозионистов и опыт практического их применения в промышленности.
Учёный | Открытие |
Р. Гадфильд | Оценка потерь металла от оксидной деструкции. Изобрёл высокопрочную сталь (Сталь Гадфильда) |
В. А. Кистяковский | Фильмовая теория коррозии |
Г. В. Акимов | Первая специализированная лаборатория |
Ю. Р. Эванс | Подробно изучил причины ускоренной деградации и её зависимость от кислородной доступности |
Научное изучение явления коррозии прошло длинный путь от древних методов защиты до нынешних теорий и лабораторных исследований. Знания, накопленные в этой области, важны для практики, особенно в отраслях машиностроения и металлообработки. Защитные методы, созданные на основе этих знаний, помогают ощутимо увеличить срок службы металлов и снизить экономические потери.
Окислительные машины и их роль в оценке устойчивости материалов
Окислительные машины — это специализированное оборудование, предназначенное для искусственного создания среды, способствующей окислению металлов. Они нужны, чтобы оценить стойкость вещества под воздействием агрессивной среды и сертификации продукции. Главные методы проверок включают использование солёного тумана, циклические тесты на деградацию, а также тесты на выдерживание температурных скачков и повышенной влажности.

Камеры для контроля качества позволяют:
- Моделировать окружающую деструктивную среду. Создавать условия, приближённые к эксплуатационным, что помогает предсказать долгосрочные свойства вещества.
- Проводить сравнительный анализ. Различные материалы можно тестировать в одинаковых средах, что позволяет выявить их относительную устойчивость к деградации.
- Оптимизировать защиту. Результаты диагностирования помогают разработать более эффективные методы защиты от коррозии, такие как выбор соответствующих покрытий или добавок, которые могут улучшить устойчивость вещества.
- Повышать качество продуктов. Выявлять недостатки в защитных покрытиях и самом сырье, что позволяет своевременно корректировать производственные процессы.
- Снижать риски аварий. Заранее выявленные деградационные процессы помогают предотвратить катастрофы, подобные перечисленным выше.
Преимущества испытательных установок
Преимущество | Описание |
Моделирование среды | Создание конкретных условий эксплуатации |
Сравнительный анализ | Возможность сравнения разных продуктов |
Оптимизация защиты | Разработка продуктивных мер против окисления веществ |
Повышение качества компонентов | Внесение коррективов в производственные процессы по выявленным процессам деградации |
Снижение аварийных рисков | Своевременное выявление деструктивных процессов |
Машины окислительной среды являются необходимым инструментом для оценки устойчивости веществ. Они позволяют проводить исследования в контролируемых средах, что способствует большему пониманию процессов корродирования и помогает разработать продуктивные методы защиты. В условиях растущих требований к безопасности и долговечности продуктов потребность в таких проверках становится всё более острой. Использование машин диагностирования стоит рассмотреть, как инвестицию в качество и надёжность продукции, и это может стать серьёзным шагом к снижению рисков и затрат в будущем.
Что такое коррозионные камеры и зачем они нужны?
Приборы для исследования на оксидную деструкцию — это специализированные устройства, предназначенные для тестирования сырья на устойчивость к ржавлению. Они представляют собой герметичный контейнер, внутри которого создаются контролируемые условия, характерные для эксплуатационной среды.
Главные компоненты деструкционной машины:
Компонент | Описание |
Атмосферный контроллер | Контролирует уровень кислорода и других газов |
Система увлажнения | Создаёт необходимую влажность |
Датчики температуры | Обеспечивают точный температурный контроль |
Система подачи раствора | Позволяет создавать агрессивные растворы |
Аппараты могут различаться по размеру, конструкции и типу воздействия. Например, Natural Sea Spray (NSS) применяется для моделирования влияния морской воды и солёного тумана. Это особенно актуально для кораблей и платформ, находящихся в контакте с солёной водой. Машины Accelerated Salt Spray (ASS) применяются для ускоренных тестов. Также есть комбинированные модели, позволяющие одновременно испытывать вещество на несколько видов воздействий.
Общая рабочая схема анализа на корродирование включает:
- Подготовка образца: очищение от загрязнений и маркировка.
- Размещение образца в машине: установка в резервуар с нейтральным солевым раствором или в зону солёного тумана.
- Мониторинг среды: регулировка температуры, давления, влажности и времени экспериментирования.
После завершения теста образец извлекают и подвергают тщательному анализу.
Исследователи ищут признаки деградации, на их основе оценивают его устойчивость.
Основные виды окислительных тестов
С помощью устройств испытания на ржавление проводят несколько типов тестов, каждый из которых предназначен для оценки различных аспектов коррозиестойкости.
Тест на солевой туман (NSS)
Моделирует воздействие морской воды, образцы погружаются в нейтральный солевой раствор при температуре 35°C и давлении 90 кПа. Продолжительность теста может меняться от нескольких часов до нескольких дней.
Ускоренный солевой спрей (ASS)
Заключается в цикличном воздействии солевого раствора и воздуха. При тестировании создается высококонцентрированный солёный туман. Этот метод позволяет быстро оценить устойчивость к окислению, но его результаты могут отличаться от конкретных условий эксплуатации.
Циклические коррозионные тесты
Включают в себя чередование значений температур и влажности, что позволяет выявить, как вещество ведёт себя при смене сред.
Влажность
Оценивают стойкость сырья при больших уровнях влажности, что помогает проанализировать их поведение в среде, напоминающей тропические климатические зоны.
Перепады температуры
Применяются для исследования влияния скачков температуры на устойчивость вещества к корродированию, что особенно важно для материалов, эксплуатируемых в переменчивых климатических условиях.
Эти исследования применяются в разных отраслях промышленности, включая производство автомобилей, электроники и строительного сырья. Они играют ключевую роль в обеспечении качества и долговечности производимой металлопродукции.
Зачем нужны тесты на коррозиестойкость
Испытания на корродирование много значат для контроля качества материалов. В частности:
- Гарантирование безопасности. Неправильный выбор сырья может привести к авариям и опасным последствиям. Тестирования помогают избежать этого, повышая надёжность конструкций.
- Соблюдение стандартов. Многие отрасли требуют строгого соблюдения международных нормативов. Тесты помогают подтвердить соответствие вещества этим требованиям, что является обязательным для сертификации.
- Оптимизация производственных процессов. Результаты диагностирований могут быть использованы для улучшения технологии производства и выбора более устойчивых компонентов, что в итоге снизит затраты на гарантийное обслуживание.
Для проведения оксидных тестов применяются международные стандарты International Organization for Standardization (ISO) и государственные American Society for Testing and Materials (ASTM), NACE, ГОСТ (Государственные стандарты России).
Стандарты для коррозионных испытаний
Стандарт | Описание |
ISO 9227:2022 |
Апробирование на коррозию в искусственной атмосфере. Тестирования в соляном тумане. |
ISO 3651-1:1998 ISO 3651-2:1998 |
Определение стойкости к межкристаллитной коррозии нержавеющих сталей. То же, но в отношении ферритных, аустенитных и ферритно-аустенитных (двухфазных) нержавеющих сталей в среде, содержащей серную кислоту. |
ASTM G85-2019 | Стандартная практика тестирований модифицированного солевого тумана. |
ANSI/NACE SP0502-2010 | Методика прямой оценки внешней коррозии трубопровода. |
ГОСТ 6032-2017 | Стали и сплавы коррозионностойкие. Методы проверок на стойкость против межкристаллитной коррозии. |
ГОСТ 9.908-85 | Единая система защиты от коррозии и старения (ЕСЗКС). Металлы и сплавы. Методы определения показателей коррозии и коррозионной стойкости. |
ГОСТ 9.602-2016 | ЕСЗКС. Сооружения подземные. |
ГОСТ 9.101-2002 | ЕСЗКС. Основные положения. |
ГОСТ Р 51164-98 | Трубопроводы стальные магистральные. Антикоррозионная защита. |
ГОСТ 26501-85 | Корпуса морских судов. Общие требования к электрохимической защите. |
ГОСТ 9.301-86 | ЕСЗКС. Покрытия металлические и неметаллические неорганические. Технические требования. |
ГОСТ 26251-84 | Протекторы для защиты от окисления. Технические условия. |
Для проверки коррозиестойкости продукта и компонентов, которые будут неоднократно подвергаться воздействию агрессивной среды, регулярное тестирование является инвестиционной необходимостью.
Главные параметры выбора профессиональной коррозионной камеры
Выбор окислительной установки — это серьёзный шаг для практиков, занимающихся испытанием материалов на коррозиестойкость. Богатый выбор моделей и технологий затрудняет нужный выбор. В этом разделе рассмотрим главные параметры, на которых нужно заострить внимание при поиске окислительной машины.
Первым шагом при выборе аппаратуры должно стать чёткое понимание, какие типы диагностирования планируется проводить. Важно найти аппарат, который будет соответствовать поставленным задачам.
Главные типы испытаний:
- Солёный туман. Этот вид исследования используется для проверки устойчивости веществ к воздействию солёной воды. Имитируются среды, характерные для морских и прибрежных зон.
- Циклические проверки. Включают чередующиеся периоды увлажнения и сушки, что позволяет смоделировать условия ожидаемой эксплуатации продукта.
- Диагностирование на влажность. Используется для оценки поведения компонента в условиях высокой влажности, характерных для тропического климата.
- Перепады температур. Позволяют проверять вещества на устойчивость к резким изменениям температуры, что применимо для продуктов, работающих в экстремальных климатических условиях.
Параметр | Описание |
Функционал | Для этого сначала определите виды тестов. |
Ёмкость аппарата |
Величина камеры определяет размеры образцов и их количество, которые можно проверить одновременно. При этом нужно учесть объёмы тестирований и возможности обработки. Ещё обратите внимание на масштабируемость системы и добавления дополнительных модулей. |
Диапазон температур |
Машины должны поддерживать терморежим от -20°C до +60°C. Это позволит проводить диагностирование в условиях, приближённых к ожидаемым — то есть реальным. |
Уровень влажности | Она должна регулироваться от 20 до 98%. Чем точнее поддерживаются нужные параметры, тем более репрезентативными будут результаты проверок. |
Регулировка условий | Возможность точной настройки температуры, влажности и времени исследования критична для достижения прецизионных и состоятельных результатов. |
Наличие автоматизированных систем управления | Современные аппараты должны иметь интегрированные системы самообслуживания, которые автоматизируют производство для уменьшения человеческого вмешательства и увеличения точности. |
Возможность многоступенчатых циклов | Эта функция позволяет настраивать среду испытаний, чередуя разные параметры, что более точно моделирует среду эксплуатации продукта. |
Соответствие международным стандартам | Оборудование для контроля материалов не должно противоречить стандартам ASTM, ISO, NACE и ГОСТ, что даст нужное качество тестирований и точность результатов. |
Материал конструкции | Вещество, из которого сделан аппарат, не должно быть подвержено оксидной деградации. Например, из нержавеющей стали или со специальным пластиковым покрытием. Это нужно для долговечности оборудования. |
Лёгкость использования | Выберите агрегат, который несложный в эксплуатации и прост для обслуживания. |
Цена | Учитывайте стоимость агрегата и эксплуатационные расходы. |
Проверка этих характеристик позволит избежать неоправданных финансовых расходов и потери времени на повторное тестирование.
Функциональные возможности и автоматизация окислительных машин
Автоматизированные системы управления позволяют контролировать все процессы без вмешательства оператора. Это касается настройки режимов работы, мониторинга температуры, влажности, концентрации реагентов и прочих нужных параметров.
Функция | Описание |
Наличие микрокомпьютера | Микрокомпьютеры интегрированы в аппарат, что позволяет настроить и мониторить параметры испытаний в сетевом режиме. |
Интерфейсы и программное обеспечение | Современные машины оснащаются интуитивно понятными интерфейсами и ПО, позволяющим легко настраивать и отслеживать ход исследований. Ряд производителей подключают удалённый доступ, что позволяет контролировать работу машины из любой точки мира. |
Метод распыления | Автоматизированные системы распыления обеспечивают равномерное распределение солёного тумана на образцы, что критично для достоверности результатов проверок. |
Наличие сборщика тумана | Сборщики тумана помогают предотвратить загрязнение и улучшить условия опыта, позволяя повторно использовать солевой раствор. |
Контрольный регулятор температуры | Система контролирует и поддерживает заданные температурные параметры, что необходимо для нужной точности и надёжности тестов. |
Некоторые установки имеют следующие дополнительные функции:
- Система рециркуляции воздуха для поддержания заданной среды внутри станка.
- Устройства для образования туманов переменной плотности и состава.
- Сенсоры для измерения pH, электропроводимости и других параметров среды.
- Модули для проведения комбинированных испытаний (например, одновременное воздействие солёного тумана и ультрафиолетового излучения).
Эти функции упрощают работу с окислительными агрегатами и делают процессы исследований более продуктивными и надёжными.
Выбор профессиональной окислительной установки
Подбор исследовательского-диагностического оборудования — это инвестиция в качество любого производства. При этом должны учитываться и текущие задачи, и будущее развитие лаборатории. Нужно учесть следующие аспекты:
- Изучите характеристики моделей. Проверьте совместимость устройства с методами испытаний и соблюдение всех нужных параметров, таких как температура, влажность и ёмкость.
- Репутация производителя. Нужный выбор — это приборы популярных компаний, которые предлагают надёжные решения, соответствующие международным стандартам.
- Рассчитайте бюджет. Хотя большие траты выглядят необоснованными, инвестиции в классные машины дадут возможность избежать дополнительных расходов на повторные проверки и исправление проблем с окислительной деградацией веществ в будущем.
- Сервисное обслуживание. Убедитесь, что производитель гарантирует адекватное техническое обслуживание и поддержку. Это важно для минимизации времени бездействия станков.
Корректно выбранные приборы улучшат точность проверок и улучшит интегральную производительность предприятия. Для консультаций и получения дополнительной информации обратитесь к экспертам по испытательному оборудованию. Компания «Суперайс» поставляет коррозионные камеры для промышленного применения производствам, лабораториям и частным лицам с 2013 года.
Обзор профессиональных камер для испытания на коррозию оборудования из каталога «Суперайс»
В наше время способность материалов противостоять корродированию имеет главное значение для производственных предприятий и исследовательских центров. Для объективной оценки этого показателя используются специализированные агрегаты испытаний на ржавление. Выбрать нужное оборудование можно в каталоге компании «Суперайс».
Компания «Суперайс» — это надёжный поставщик испытательного оборудования с более чем 11-летним стажем работы. Благодаря строгому соблюдению стандартов качества, компания активно сотрудничает с 5500 партнёрами и предоставляет свыше 10 000 видов товаров.
В этом разделе рассмотрены модели, представляющие группы по предпочтениям, условно выделенные из каталога: для небольших, больших и специализированных лабораторий или предприятий.
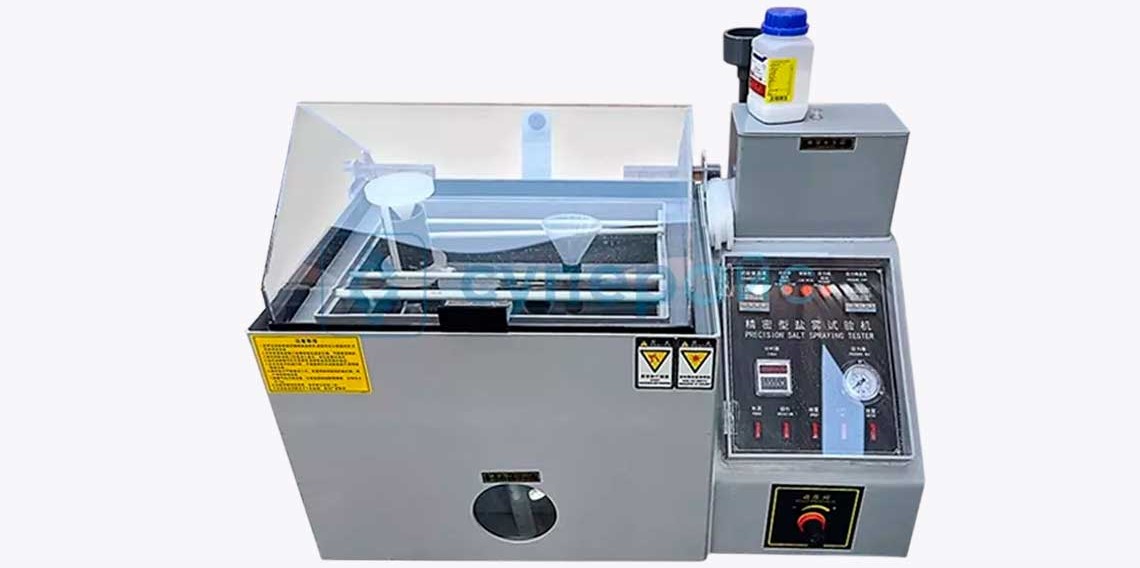
Вид тестирования | aэрозоль солевой NSS/ACSS |
Распыление | программируемое |
Температурная равномерность | ± 2℃ |
Размер тестировочной ёмкости | 47 л |
Размер сосуда для солевого раствора | 8 л |
Долив солевого раствора | ручной |
Функционал | |
Регулировка распыления | есть |
Сборка тумана | есть |
Радиатор отопления | есть |
Измерительное ведро | есть |
Сосуд для гидроизоляции | диаметр 50 мм |
Сосуд с обогащённым воздухом | есть |
Тестовая крышка | есть |
Манометр | есть |
Труба выхлопная | диаметр 48 мм |
Кран сливной | есть |
Контрольный терморегулятор | есть |
Терморегулятор цилиндра насыщения | есть |
Таймер | 0,1–999 ч |
Кнопка включения | есть |
Кнопка управления | есть |
Кнопка запуска таймера | есть |
Общие характеристики | |
Рабочее напряжение питания | 220 В |
Мощность | 2 кВт |
Внутренний размер испытательной камеры | 400х350х300 мм |
Габариты установки | 860х490х630 мм |
Габариты упаковки | 940х610х675 мм |
Вес, нетто | 35 кг |
Модель Tengfei 40 разработана с акцентом на лёгкость использования и доступность. Она удачно подходит для небольших лабораторий или предприятий, где необходима срочная проверка на стойкость к корродированию.
Преимущества:
- компактные размеры: актуально для ограниченных пространств;
- лёгкость в эксплуатации: не требует специальных навыков для управления;
- небольшие эксплуатационные расходы: экономия на обслуживании.
Эта машина станет верным выбором для тех, кто ищет доступное решение для базовых исследований.
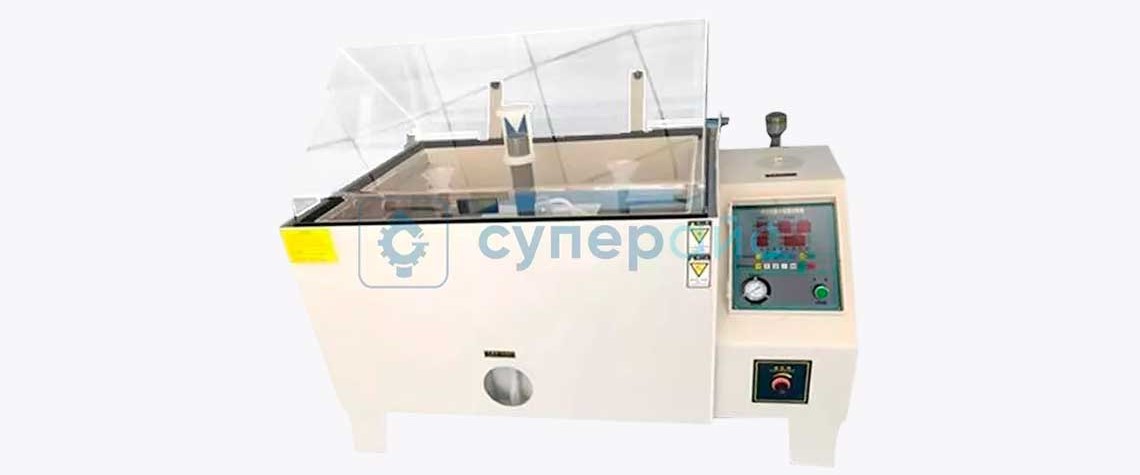
Вид тестирования | aэрозоль солевой NSS/ACSS |
Распыление | непрерывный |
Температурная равномерность | ± 2℃ |
Размер тестировочной ёмкости | 270 л |
Размер сосуда для солевого раствора | 25 л |
Долив солевого раствора | ручной |
Микрокомпьютер | есть |
Функционал | |
Регулировка распыления | есть |
Сборка тумана | есть |
Радиатор отопления | есть |
Измерительное ведро | есть |
Сосуд для гидроизоляции | диаметр 50 мм |
Сосуд с обогащённым воздухом | нет |
Тестовая крышка | нет |
Манометр | есть |
Труба выхлопная | диаметр 48 мм |
Кран сливной | есть |
Контрольный терморегулятор | есть |
Терморегулятор цилиндра насыщения | есть |
Таймер | 0,1–999 ч |
Кнопка включения | есть |
Кнопка управления | есть |
Кнопка запуска таймера | есть |
Общие характеристики | |
Рабочее напряжение питания | 220 В |
Мощность | 2 кВт |
Внутренний размер испытательной камеры | 900х500х600 мм |
Габариты установки | 1340х820х1080 мм |
Габариты упаковки | 1410х890х1100 мм |
Вес, нетто | 75 кг |
Модель Tengfei 90 предлагает пользователям точность в настройке параметров испытаний благодаря интеграции с микрокомпьютером. Это делает её рациональным вариантом оборудования для лабораторий и заводов, которые проводят сложные и разнообразные тесты.
Преимущества:
- в программируемом режиме пользователи могут задать персональные параметры тестирования;
- микрокомпьютер обеспечивает стабильность условий высокоточных исследований;
- результаты тестов можно сохранять и анализировать.
Эта машина подходит для лабораторий с передовым оснащением и предприятий, которые ставят перед собой задачи по глубинному анализу стойкости к корродированию материалов.
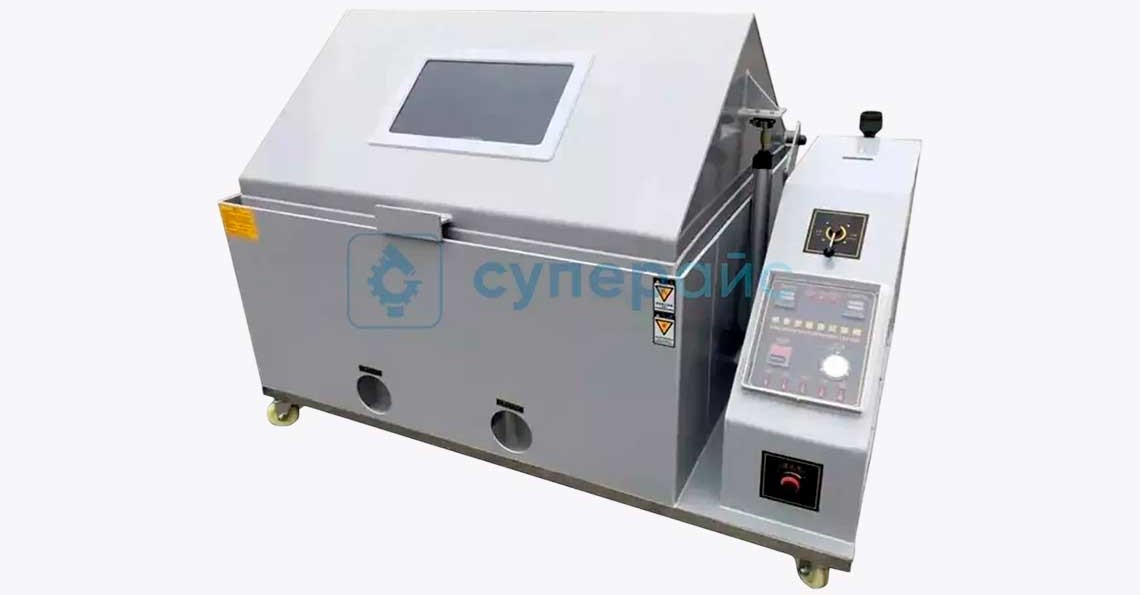
Вид тестирования | cолевым аэрозолем NSS/ACSS |
Распыление | программируемый |
Температурная равномерность | ± 1℃ |
Размер тестировочной ёмкости | 800 л |
Размер сосуда для солевого раствора | 45 л |
Долив солевого раствора | ручное/автоматическое |
Пневматическое открывание камеры | есть |
Функционал | |
Регулировка распыления | есть |
Сборка тумана | есть |
Радиатор отопления | есть |
Измерительное ведро | есть |
Сосуд для гидроизоляции | диаметр 50 мм |
Сосуд с обогащённым воздухом | есть |
Тестовая крышка | есть |
Клапанное регулирование давления | регулируется только во время испытания (1 кг/см²) |
Манометр | есть |
Труба выхлопная | диаметр 48 мм |
Кран сливной | есть |
Контрольный терморегулятор | есть |
Терморегулятор цилиндра насыщения | есть |
Таймер | 0,1–999 ч |
Кнопка включения | есть |
Кнопка управления | есть |
Кнопка запуска таймера | есть |
Общие характеристики | |
Дисплей | сенсорный экран |
Рабочее напряжение питания | 220 В |
Мощность | 2 кВт |
Внутренний размер испытательной камеры | 1600х1000х500 мм |
Габариты установки | 2300х1300х1400 мм |
Габариты упаковки | 2500х1500х1600 мм |
Модель Tengfei 160 ориентирована для обширных исследований, где требуется прецизионная точность и контроль заданных условий.
Преимущества:
- большой размер испытательной ёмкости позволяет тестировать несколько образцов одновременно, что ощутимо экономит время на испытания;
- усиленная степень автоматизации повышает точность и качество проверки за счёт уменьшения участия человека;
- интуитивно понятный интерфейс облегчает работу и обучение новых сотрудников;
- надёжность в средах больших уровней влажности.
Эта машина подойдёт для больших производств и лабораторий, где необходимы регулярные проверки на корродирование.
Выбор оборудования для испытаний на оксидную деструкцию — это стратегическое решение, влияющее на результаты тестирования. Каждая из представленных из «Суперайс» моделей предлагает собственные преимущества, что позволяет принять нужное решение в зависимости от требований вашего производства.
Компания «Суперайс» гарантирует требуемое качество продукции и обеспечивает клиентов технической поддержкой, а также услугами послепродажного обслуживания. Для получения дополнительных советов и консультаций по использованию оборудования обращайтесь к нашим консультантам через официальный сайт.
Выбор окислительной машины — серьёзный шаг для организаций, стремящихся обеспечить надёжность своих материалов и долговечность конструкций. Профессиональное оборудование для испытания коррозии позволяет оценить стойкость к окислению и улучшить производственные циклы, снижая риски, связанные с деградацией металлов. Рассмотрим главные параметры, требующие внимания при выборе окислительной установки.
Параметр выбора | Описание |
Тип аппарата |
Определите нужный вид устройства для ваших испытаний: NSS (для имитации морского климата) или ASS (для ускоренных тестов) |
Размер и функционал | Выбор между компактными экономичными аппаратами для малых предприятий и более крупными моделями с расширенными возможностями для лабораторий |
Объём рабочего пространства | Убедитесь, что размеры аппарата соответствуют количеству образцов, которые вы планируете тестировать одновременно |
Управление и автоматизация | Наличие функционального интерфейса и автоматизированных режимов облегчает проведение экспериментов |
Материалы конструкции | Выбирайте агрегаты из износостойких компонентов для увеличения срока службы |
Сервис | Уточните условия гарантии и доступность сервисного обслуживания |
Тщательно выбранная окислительная машина — это не только инструмент, это и помощник в лаборатории или производственном цикле. Устройство должно быть адаптировано под требуемые специфические нужды, чтобы обеспечить точность и повторяемость результатов.