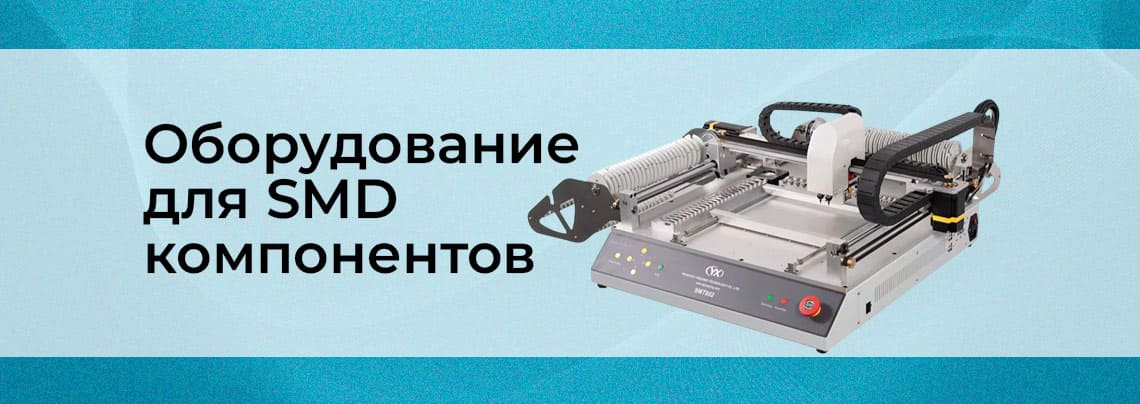
В далёкие шестидесятые годы, когда трава была зеленее, а электронные устройства ещё вовсю конструировались и изготавливались на вакуумно-электронных лампах и навесной монтаж был также популярен, как печатный, была разработана необычная по тем временам технология пайки компонентов на медные контактные площадки (полигоны) печатных плат. Она стала именоваться технологией поверхностного монтажа (ТПМ) в русскоязычной литературе, и, аналогично, surface-mount technology (SMT) в англоязычной. ТПМ подарила более высокую плотность в сочетании с ускорением и удешевлением сборки. Это изобретение немного опережало время: в шестидесятые годы электронная промышленность ещё не была готова к выпуску компонентов для SMT: степень миниатюризации была тогда почти нулевая, в плотность размещения во времена, когда относительно огромные электровакуумные лампы ещё прочно сидели в головах конструкторов электроаппаратуры, ещё не учитывалась. Да и общее машиностроение не давало электронной промышленности специализированное оборудование ТПМ. Поверхностный монтаж применялся только при выпуске спецаппаратуры, в частности, для военной или аэрокосмической отраслей.
Но с середины восьмидесятых ситуация стала меняться: начался бурный расцвет SMT-технологии. Появились миниатюрные резисторы, конденсаторы, транзисторы, диоды, микросхемы и всё остальное, разработанное для пайки с применением SMT. Все они стали называться surface-mount devices (SMD). Параллельно стали появляться машины для их установки, так как к ручной пайке они были слабо приспособлены. Толчком к взрывному развитию послужила тенденция к общему удешевлению электронной продукции, уменьшению её габаритов и массы.
Статья ставит целью дать общее представление о технологии SMT и о самих SMD; кратко расскажем об особенностях и конструкции оборудования, применяемого в SMT, сделаем обзор нескольких современных станков, предлагаемых изготовителями, и успешно работающих на малых и крупных предприятиях в мире.
Время чтения: 25 минут
Станки для монтажа SMD компонентов? Это очень просто!
Технология поверхностного монтажа (SMT)
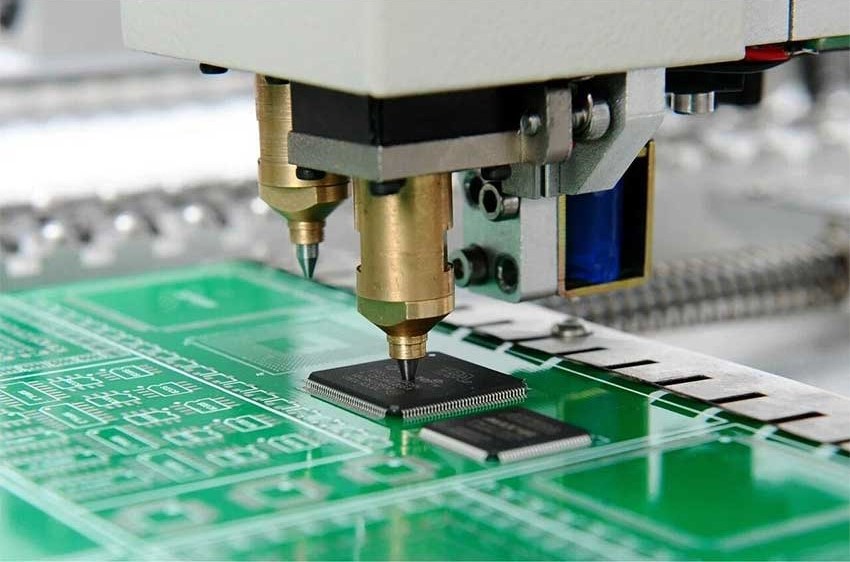
Технология surface-mount technology (SMT) берёт своё начало ещё с шестидесятых годов XX века. В это время ещё очень активно проектировалась и промышленно выпускалась аппаратура, где основой служили радиолампы; а полупроводниковые электронные приборы только-только входили в массовое производство; выпуск отдельных видов микросхем уже налажен, но исключительно для спецаппаратуры военного или аэрокосмического назначения. Именно военно-космические отрасли, наиболее бурно развивавшиеся в условиях холодной войны и космической гонки, стали активно соревноваться в уменьшении габаритов, массы и энергопотребления аппаратуры. Одним из методов решения такой инженерной задачи стало уменьшение размера элементной базы и увеличение плотности её расположения.
Электронная промышленность середины двадцатого века ещё вовсю использовала навесной монтаж на специальные монтажные стойки и/или непосредственно между собой. Он требовал множества ручных операций. А ещё применялся печатный монтаж выводных компонентов в отверстия (through hole technology, THT), который серьёзно автоматизировался. Не говоря о первом, даже второй способ не давал высокую плотность: выводные элементы довольно крупногабаритны, требуют много места. Печатные платы тогда приходилось просверливать множеством отверстий, в которых посредством выводов элементы крепились и электрически соединялись.
Все выявленные недостатки требовали устранения: ТПМ-технология стала решением всех проблем. Её суть в пайке спецкомпонентов не на монтажные стойки или продевание гибких выводов через отверстия, а напрямую на полигоны, расположенные с той же стороны, что и дорожки на печатной плате. Их стали называть компонентами для поверхностного монтажа (surface-mount devices, SMD).
Технология предоставила преимущества:
- Устраняется необходимость такой технологической операции, как сверление отверстий, а медные контактные площадки для пайки вытравливаются вместе с дорожками (смотри статью «Проектируем печатную плату»).
- Отсутствие выводов уменьшает габариты с весом элементов, следовательно, стоимость.
- Менее материалоёмкие и недорогие компоненты получается создавать быстрее, причём очень объёмными партиями.
- Малогабаритные решения помогают увеличить плотность монтажа (разместить больше элементов на определённой площади платы).
- В случае двухсторонней платы возможно размещение с обеих сторон, что ещё дополнительно увеличивает плотность размещения.
- Выбор этой технологии снижает размеры, вес и стоимость готового устройства.
- Помимо группового изготовления печатных плат, стала возможна групповая пайка компонентов, дополнительно снижающая сроки изготовления устройств с их себестоимостью.
- Появилась возможность автоматизации процесса размещения, пайки и контроля компонентов.
Как следует из перечня преимуществ, SMT-технология способна стать просто «золотой страной Эльдорадо» для изготовителей электроники. Так оно и стало, но годы спустя. Ну а в шестидесятые, о которых идёт речь, её массового использования не произошло, так как были некоторые немаловажные моменты:
- Электронная промышленность середины двадцатого века не умела разрабатывать и массово изготавливать SMD. Разработки и выпуск велось только для «затратных» по определению отраслей: космонавтики и армии. В массовой аппаратуре SMT не применялся.
- Миниатюризация компонентной базы привела к принципиальной невозможности ручной пайки и потребовала разработки с внедрением спецоборудования — станков для автоматизированного монтажа.
Эти моменты были решены в частном порядке для внедрения ТПМ в военной и аэрокосмической отрасли, но в массовой аппаратуре это случилось только в восьмидесятых. В это время ТПМ стала повсеместно доступной, начался массовый выпуск компонентов для применения в этой технологии, а также появились относительно недорогие, но производительные станки для автоматизированного монтажа (pick-and-place machines, P&P). О SMD и станках будет рассказано в посвящённых им разделах статьи.
В общем, вся SMT-технология состоит из пяти этапов:
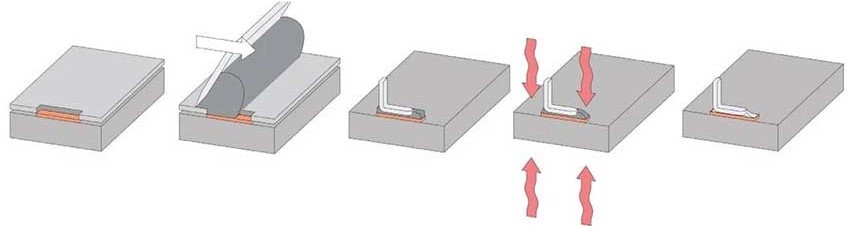
Этап 1. На печатную плату накладывается специальный трафарет из тонкого листа нержавеющей стали с прорезями, расположенные в точности над контактными площадками для пайки. Этот трафарет, как и печатная плата, легко проектируются в системах автоматизированного проектирования (САПР) и изготавливаются на спецпроизводствах.
Этап 2. На печатную плату наносится паяльная паста, состоящая из припоя и флюса (смотри статью «Несколько слов о флюсах для пайки»). Она попадает через прорези в трафарете только на нужные контактные площадки.
Этап 3. Трафарет изымается. С помощью P&P-станка компоненты размещаются над контактными площадками и фиксируются клеящей способностью паяльной пасты.
Этап 4. Выполняется пайка. Паяют несколькими способами, где самым популярными стала термовоздушная пайка на специальных нагревательных столах, а в условиях массового изготовления в паяльных печах.
Этап 5. Включает визуальный контроль качества с проверкой электрических параметров паяного соединения.
Компоненты для поверхностного монтажа (SMD)
Это специализированные миниатюрные и сверхминиатюрные электронные компоненты для SMT. Не путайте эти два понятия: Surface-mount technology (SMT) — это общее наименование технологии, а surface-mount devices (SMD) — это название группы электронных компонентов, применяемых в SMT-технологии.
Сегодня практически все детали реализуемы в форм-факторе SMD, кроме тех, которые ввиду конструктивных особенностей не бывают миниатюрными: мощные резисторы (смотри статью «Как проверить резистор мультиметром?»), высоковольтные конденсаторы (смотри статью «Как выбрать конденсатор?»), силовые дроссели, трансформаторы, некоторые коммутационные изделия, такие как разъёмы, реле и тому подобные. Многие до сих пор выпускаются как в выводном исполнении, так и для SMT. В таблице ниже представлены наиболее часто используемые SMD компоненты и описание их разновидностей:
![]() |
Резисторы: |
![]() |
Конденсаторы: |
![]() |
Катушки индуктивности (дроссели): |
![]() |
Диоды: |
![]() |
Светоизлучающие диоды: |
![]() |
Кварцевые резонаторы: |
![]() |
Транзисторы: |
![]() |
Микросхемы: |
![]() |
Предохранители: |
![]() |
Разъёмы: |
SMD получили множество типоразмеров, что обусловлено разнообразным назначением, внутренним устройством, количеством выводов и другими особенностями. Ниже будут перечислены основные. Сведения, представленные ниже, потребуются для понимания некоторых моментов в следующих разделах статьи.
В зависимости от размера, пассивные SMD, такие как резисторы, конденсаторы и катушки индуктивности делятся на следующие типоразмеры:
Типоразмер |
Размер в миллиметрах (длина*ширина) |
01005 |
0,4*0,2 |
0201 |
0,6*0,3 |
0402 |
1,0*0,5 |
0603 |
1,6*0,8 |
0805 |
2,0*1,25 |
1206 |
3,2*1,6 |
1210 |
3,2*2,5 |
1812 |
4,5*3,2 |
1825 |
4,5*6,4 |
2220 |
5,6*5,0 |
2225 |
5,6*6,3 |
Электролитические конденсаторы делятся так:
Типоразмер |
Размеры цилиндра конденсатора в миллиметрах(диаметр*высота) |
Размеры основания конденсатора в миллиметрах (длина=ширина) |
0505 |
5*5,4 |
5,3 |
0605 |
6,3*5,4 |
6,6 |
0607 |
6,3*7,8 |
6,6 |
0810 |
8*10 |
8,0 |
1008 |
10*8 |
10,3 |
1010 |
10*10 |
10,3 |
1213 |
1,5*13,5 |
13,6 |
1216 |
12,5*16 |
13,6 |
1616 |
16*16,5 |
16,3 |
Типоразмеры танталовых твердотельных конденсаторов:
Типоразмер |
Габариты корпуса в миллиметрах (длина*ширина) |
A |
3,2*1,6*1,6 |
B |
3,5*2,8*1,9 |
C |
6,0*3,2*2,2 |
D |
7,3*4,3*2,4 |
E |
7,3*4,3*4,1 |
Диоды получили следующие типы корпусов:
Наименование корпуса |
Габариты корпуса в миллиметрах (длина*ширина) |
SOD923 |
0,8*0,6 |
SOD723 |
1,0*0,6 |
SOD523 |
1,2*0,8 |
SOD323 |
1,7*1,25 |
SOD123 |
2,7*1,5 |
DO215AC |
4,3*2,6 |
DO215AA |
4,3*3,6 |
DO215AB |
7,0*6,0 |
SMAJ |
4,3*2,6 |
SMBJ |
4,3*3,6 |
SMCJ |
7,0*6,0 |
Светоизлучающие диоды получили типоразмеры:
Типоразмер |
Габариты корпуса в миллиметрах (длина*ширина) |
Количество кристаллов |
3014 |
3,0*1,4 |
1 |
2835 |
2,8*3,5 |
1 |
3528 |
3,5*2,8 |
1/3 |
5050 |
5,5*1,6 |
3/4 |
5630 |
5,6*3,0 |
1 |
5730 |
5,7*3,0 |
1/2 |
Полупроводниковые транзисторы и некоторые виды микросхем выпускаются в следующих корпусах:
Наименование корпуса |
Количество выводов |
Габариты корпуса в миллиметрах (длина*ширина*высота) |
SOT723 |
3 |
1,2*0,8*0,5 |
SOT346 |
3 |
2,9*1,6*1,1 |
SOT323 |
3 |
2,0*1,25*0,9 |
SOT416 |
3 |
1,6*0,8*0,7 |
SOT523F |
3 |
1,6*0,8*0,7 |
SOT23 |
3 |
2,9*1,3*0,95 |
SOT23-5 |
5 |
2,9*1,6*1,1 |
SOT23-6 |
6 |
2,9*1,6*1,1 |
SOT89 |
3 |
4,5*2,5*1,5 |
SOT143 |
4 |
2,9*1,6*0,95 |
SOT223 |
3 |
6,5*3,6*1,6 |
SOT323 |
3 |
2,0*1,25*0,9 |
SOT343 |
4 |
2,0*1,25*0,9 |
SOT353 |
5 |
2,0*1,25*0,9 |
SOT363 |
6 |
2,0*1,25*0,9 |
SOT23-8 |
8 |
2,9*1,6*1,2 |
DPAK |
3 |
6*6,5*2,3 |
D2PAK |
3 |
9,2*10*4,4 |
D2PAK-5 |
5 |
9,2*10*4,4 |
D2PAK-7 |
7 |
9,2*10*4,4 |
D3PAK |
3 |
14*16*4,7 |
Корпуса микросхем получили богатую номенклатуру. В таблице ниже будут перечислены часто используемые с указанием характерных особенностей:
Наименование корпуса |
Характерные особенности |
2 ряда выводов | |
SOIC |
Дистанция между выводами 1,27 мм |
TSOP |
Тоньше SOIC, дистанция 0,5 мм |
SSOP |
Уменьшенный SOIC, на 0,65 мм |
TSSOP |
Тоньше SSOP, дистанция аналогична |
QSOP |
В четыре раза меньше SOIC, дистанция 0,635 мм |
VSOP |
Меньше QSOP, дистанция 0,4/0,5/0,65 мм |
4 ряда выводов | |
PLCC/CLCC |
Пластиковый/керамический корпус, дистанция между выводами 1,27 миллиметра, выводы загнуты в форме литеры J |
QFP |
Квадратные плоские корпуса различного размера (в зависимости от количества выводов) |
LQFP |
Тонкий QFP (1,5 миллиметра) |
PQFP/TQFP |
Пластиковый/керамический корпус с количеством выводов не менее 44 |
TQFP |
Тонкий QFP (1,1 миллиметра) |
PQFN |
QFP с площадкой для отвода тепла |
Массив шариковых и столбиковых выводов или контактных площадок | |
BGA |
Массив шариковых выводов, дистанция между выводами 1,27 миллиметра |
LFBGA |
Тонкий BGA, дистанция между выводами 0,8 миллиметра |
CGA/CCGA |
Пластиковый/керамический корпус, массив столбиковых выводов |
uBGA |
BGA с уменьшенной дистанцией между выводами (менее 1 миллиметра) |
FCBGA |
Подложка с массивом шариковых выводов с припаянным к ней кристаллом и теплораспределителем |
LLP |
Корпус с контактными площадками |
Оборудование для монтажа
Развитие техники для установки SMD, как самой SMT-технологии, берёт начало в шестидесятых годах двадцатого века. Как было сказано ранее, тогда машиностроение не было готово предложить решения для автоматизации ТПМ, и процесс их позиционирования и пайки в общем был ручным, то есть монотонным, трудоёмким, сопряжённым с множеством ошибок. Первые примитивные станки, появившиеся в то время, показывали низкую производительность и монтировали лишь нескольких единиц в минуту, что при «микросерийном» выпуске для космонавтики и военных было вполне приемлемо. Но при нормальном серийном изготовлении массовой продукции требуется производительность выше на несколько порядков.
Так в восьмидесятых годах появляется новое поколение относительно высокоскоростных машин для автомонтажа SMD. Их особенностью было то, что одна машина монтировала детали только одного типа, а при необходимости установки нескольких типов компонентов требовалось соответствующее количество машин, объединённых наподобие конвейера: после выполнения своей операции одна передвигала плату к другой и так далее.
Важно понимать, что в восьмидесятые годы даже они стоили запредельно, а ставить несколько таких машин, а то и несколько десятков, было доступно только компаниям мирового уровня. К тому же многократное последовательное перемещение платы плохо сказывалось на её качестве (элементы смещались от тряски и вибрации при перемещении; возможна была пайка лишь лёгких деталей), а также на производительности в целом.
В девяностые годы на рынке появились станки, устанавливающие нескольких SMD-типов путём автоматической смены вакуумных захватов-сопел. Это резко увеличивало производительность и снижало себестоимость изготовления продукции. В это время монтажное оборудование стало снабжаться машинным зрением (смотри статью «Несколько слов о робототехнике»), дающим автоматический визуальный контроль наличия элемента и соответствия технологическому процессу, с коррекцией его положения при размещении.
В двухтысячные годы оборудование стало снабжаться несколькими соплами-захватами с отдельными для каждого высокоскоростными приводами, что дало возможность параллельного размещения деталей. Наиболее совершенные машины этого периода достигали производительности более 100000 комп/час. Сегодня развитие производственных технологий привело к резкому снижению стоимости STM-машин и быстрой окупаемости, даже в условиях мелкосерийной сборки, не говоря уже о массовом выпуске в условиях крупного предприятия. Также небольшая цена позволяет покупать их ВУЗам для использования в образовательно-практической сфере.
Станки состоят из нескольких комплексных систем:
- Система подачи плат и элементов. Многие имеют такую систему, созданную для загрузки и выгрузки плат, перемещения и подготовки компонентов (к примеру, снятия упаковочной плёнки с ленты с ними), а также для их подачи непосредственно в размещающую головку. Эта система использует конвейеры, питатели и механические или роботизированные устройства.
- Система управлением движением. Абсолютно все станки оснащаются высокоточными трёхосевыми приводами позиционирования размещающей головки. В систему входят шаговые серводвигатели (или электродвигатели других типов, например, линейные), контроллеры этих двигателей, электронный блок управления и программное обеспечение. Она бывает комбинированной и содержат гидравлические или пневматические приводы (работающие от сжатого воздуха или вакуума).
- Система размещающих головок. Современные станки имеют от одной до нескольких размещающих головок с собственными приводами и/или систему автоматической замены размещающей головки, если привод единственный. Система размещающих головок использует вакуумный, механический или иной привод захвата.
- Система машинного зрения. Многие станки используют её для обнаружения, идентификации радиокомпонента, первичной дефектовки, разворота и позиционирования. Система состоит из камеры высокого разрешения и программной среды для распознавания образов, анализирующей изображение, определяющей положение и ориентацию всех элементов, включая платы.
Отдельно рассказываем о питателях — специализированной оснастки для подачи радиодеталей в станок в таком виде, в котором будет обеспечена возможность их захвата. В современном SMT-оборудовании питатель состоит из катушки с намотанной на неё лентой с радиодеталями или лотка с ними, из которого они подаются в головку захвата и размещения или другие рабочие области. Питатель обычно имеет ременной, фрикционный или вибрационный привод. Есть нескольких типов:
- Катушечный/ленточный. Используется для подачи деталей, упакованных в катушку/ленту (практически все).
- Лотковый. Здесь элементы упакованы в лотки или трубки (обычно так упаковывают крупногабаритные и дорогие).
- Насыпной. Используется для подачи никак не упакованных элементов.
Питатели являются частью процесса SMT, поскольку они создают постоянную ритмическую подачу деталей для системы захвата и размещения или другого оборудования. Это помогает собирать платы быстрее и с высокой эффективностью.
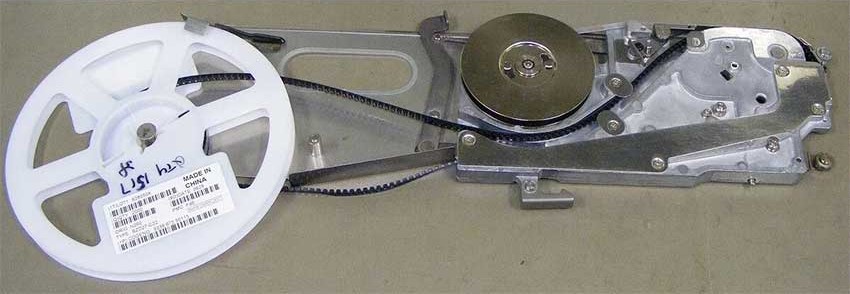
Катушка, используемая в катушечных и ленточных питателях — это специализированный вид упаковки, который помимо высокоплотного размещения предоставляет удобство работы по извлечению и подачи деталей в питатель . Она, как правило, изготавливается из пластика, а лента с элементами из картона или жёсткой плёнки. Снабжена карманами, в которых размещаются радиокомпоненты, закрытые сверху мягкой прозрачной лентой.
Катушки используют в отрасли SMT для снижения стоимости упаковки и обработки радиодеталей. Они также более компактны, чем лотки или трубки.
Обзор современного оборудования
Современные китайские фирмы-изготовители предлагают богатую номенклатуру недорогих, но высокопроизводительных настольных станков для автоматизированного монтажа SMD, которые являются прямыми конкурентами продукции американских, немецких и японских лидеров. В разделе будут описаны наиболее доступные и универсальные модели, которые успешно применимы как в небольшом частном предприятии, так и в промышленности в условиях мелко- и среднесерийного изготовления.
Серия ZB3245/ZB3545 компании Zhengbang
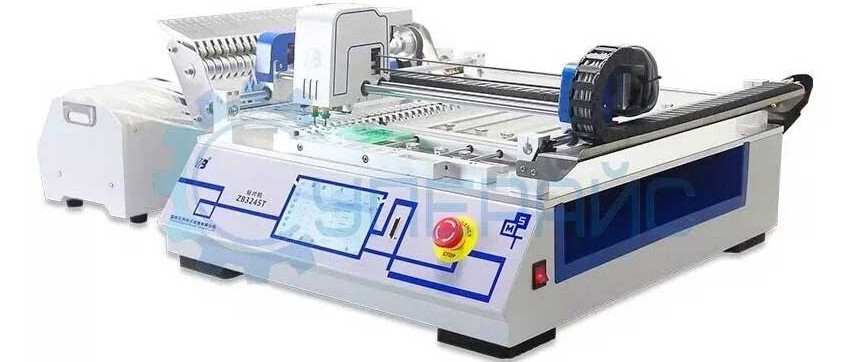
В серию входит несколько настольных станков, отличающихся как геометрическими параметрами, так и функционалом, но имеющими высокую точность позиционирования и производительность.
ZB3245T |
ZB3245TS |
ZB3245TSS |
ZB3545TPP |
|
Точность позиционирования размещающих головок (миллиметров) |
0,025 | |||
Количество размещающих головок |
2 | 4 | ||
Максимальная скорость размещения (компонентов в час) |
4000 | 6000 | 8000 | 7500 |
Количество мест для катушечных/ленточных питателей |
27 | 27 | 54 | 38 |
Количество камер системы машинного зрения |
нет | 2 | 4 | 6 |
Максимальный размер печатной платы (миллиметров) |
320*450 | 350*450 | ||
Максимальный высота монтируемых элементов |
≤10 | ≤19 | ≤12 | |
Встроенный дисплей |
да | нет | ||
Встроенный компьютер |
нет |
Это недорогие, но ультрасовременные высокопроизводительные настольные станки для SMT с программным управлением. Все они способны работать с независимыми катушечными/ленточными питателями , а также есть возможность использования вибропитателей (опционально); возможна установка компонентов от типоразмера 0402÷5050, а также микросхем в корпусах SOIC, QFP, BGA и других. Средние модели (ZB3245TS/ZB3245TSS) этой серии имеют систему машинного зрения для распознавания и позиционирования ; шесть камер старшей модели (ZB3545TP) полностью следят за процессом, сводя риск брака к минимуму. Как старшая, так и средняя и младшая модель (ZB3245T) имеют высокую производительность, эргономику, качественные комплектующие и удобное программное обеспечение, в котором легко и оперативно разрабатывается карта монтажа. Эта серия станков будет уместна как при мелкосерийном запуске, так и в образовательно-практической деятельности высших учебных заведений.
Zhengbang ZB4050LS
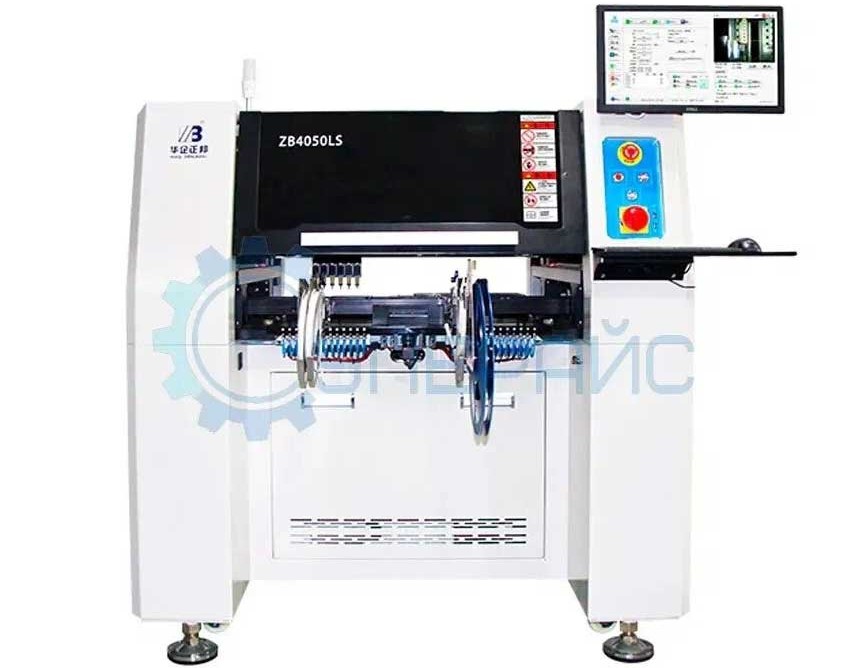
Если серия ZB3245/ZB3545 — это недорогие станки с достойными, но всё же со средними характеристиками, то машина ZB4050LS от компании Zhengbang уже для профессионального применения и исключительно надёжна, способна долго работать без перерыва и необходимости наладки.
ZB4050LS |
|
Точность позиционирования размещающих головок (миллиметров) |
0,025 |
Количество размещающих головок |
6 |
Максимальная скорость размещения (компонентов в час) |
11000 |
Количество мест для катушечных/ленточных питателей |
64 |
Количество камер системы машинного зрения |
3 |
Максимальный размер печатной платы (миллиметров) |
500*400 |
Максимальная высота монтируемых деталей |
≤6 (опционально до ≤11) |
Встроенный дисплей |
да |
Встроенный компьютер |
да |
Это классический напольный SMT-станок. Он предназначен для долговременной работы в условиях средне- и крупносерийного производства. ZB4050LS совместим с независимыми лентами или катушками в количестве до 64 . Станок оснащён системой машинного зрения с тремя камерами для автоматической визуальной инспекции всех этапов технологического процесса. Комплектуется промышленным ПК с предустановленным рабочим ПО. Шесть размещающих головок имеют исключительную производительность и предназначены для пайки деталей типоразмера 0402÷5050 и аналогичных по габаритам, а также SOIC-, QFP-, BGA-микросхем и других. Станок ZB4050LS высокопроизводителен, эргономичен, получил качественные комплектующие и удобное ПО, с которым быстро и легко запускается в работу . Модель относительно недорогая и быстро окупается.
Серия TVM802 компании QIHE
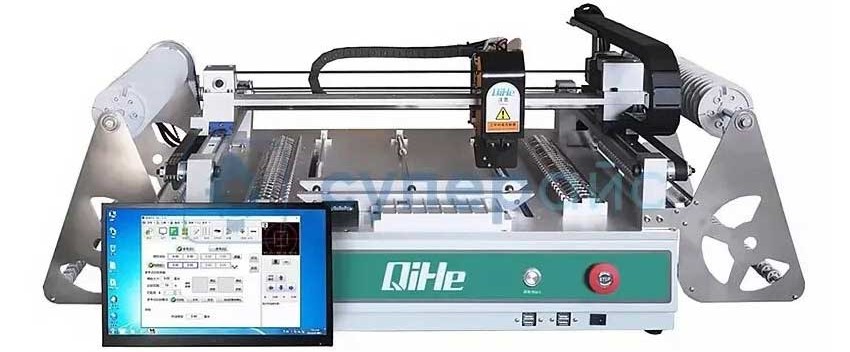
Продукция компании QIHE составляет серьёзную конкуренцию технике Zhengbang и предлагает серию высокоточных высокоскоростных настольных станков.
TVM802A |
TVM802AX |
TVM802B |
TVM802BX |
TVM802B+ |
|
Точность позиционирования размещающих головок (миллиметров) |
0,025 | ||||
Количество размещающих головок |
2 | ||||
Максимальная скорость размещения (компонентов в час) |
6500 | ||||
Количество мест для катушечных/ленточных питателей |
29 | 46 | 58 | ||
Количество камер системы машинного зрения |
2 | ||||
Максимальный размер печатной платы (миллиметров) |
340*340 | 260*340 | 300*320 | ||
Максимальный высота монтируемых элементов |
≤12,5 | ||||
Встроенный дисплей |
нет | да | |||
Встроенный компьютер |
нет | да | нет | да | да |
Машины серии TVM802 — недорогое, но многофункциональное и в чём-то даже инновационное решение с программным управлением . Все станки работают с независимыми катушечными/ленточными питателями, которых в разных моделях от 29 до 58. Все модели серии оснащены системой машинного зрения.
Модели TVM802AX, TVM802BX, TVM802B+ поставляются с промышленным компьютером с предустановленным программным обеспечением, необходимым для работы станка, а также позволяющим в режиме реального времени отслеживать основные параметры работы.
Станки этой серии созданы для установки электронных компонентов типоразмера 0402÷5050 и аналогов, микросхем в корпусах SOIC, QFP, BGA и других. Все машины серии высокопроизводительны, эргономичны, собраны на качественных комплектующих и получили удобное ПО . Они отличаются демократичной для подобного оборудования ценой и быстро окупаются.
QIHU TVM926
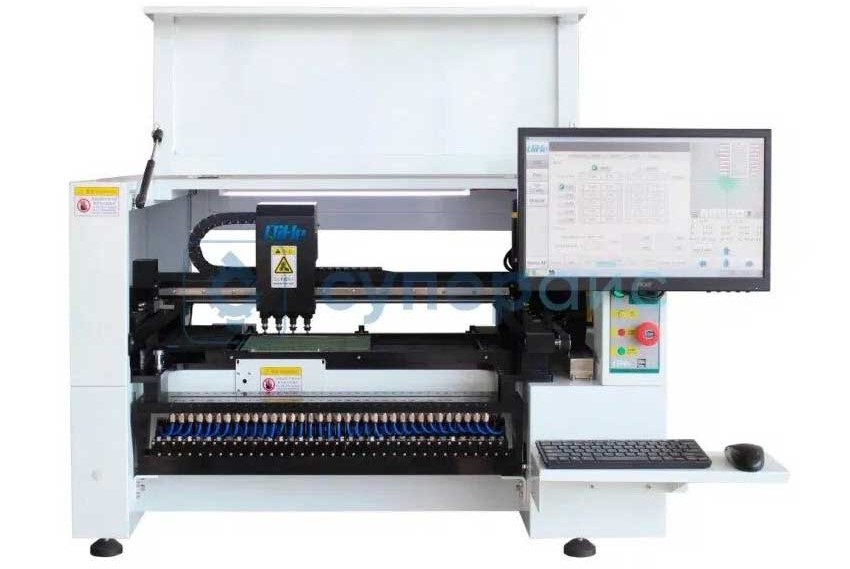
Если серия TVM802 представлена недорогими моделями с достойными, но всё же со средними эксплуатационными параметрами, то TVM926 от компании QIHU — профессиональное решение, отличающееся исключительной надёжностью , и способное беспрерывно работать без постоянной наладки.
TVM926 |
|
Точность позиционирования размещающих головок (миллиметров) |
0,025 |
Количество размещающих головок |
4 |
Максимальная скорость размещения (компонентов в час) |
9000 |
Количество мест для катушечных/ленточных питателей |
64 |
Количество камер системы машинного зрения |
6 |
Максимальный размер печатной платы (миллиметров) |
330*580 |
Максимальная высота монтируемых деталей |
≤16 |
Встроенный дисплей |
да |
Встроенный компьютер |
да |
Модель оптимальна для средне- и крупносерийного производства электроники . TVM926 поддерживает работу с независимыми катушечными/ленточными питателями числом до 64 . Установлена система машинного зрения, промышленный компьютер с предустановленным ПО для работы.
Четыре размещающих головки дают огромнейшую производительность и поддерживают типоразмер 0402÷5050 и изделия с аналогичными габаритами, корпусные микросхемы в форм-факторе SOIC, QFP, BGA и других.
Сегодня ТПМ специализированных миниатюрных SMD-деталей наиболее прогрессивна: достижения науки и техники сделали доступнее сверхплотный монтаж деталей, дали высокую степень миниатюризации и надёжности техники с одновременным ускорением её сборки и снижением стоимости. Не чудо ли?! Чудо, которым мы все с вами пользуемся каждый день: смартфоны, ноутбуки, персональные компьютеры — всё это продукты наивысшей степени развития SMT технологии.
Станки для автоматизированного монтажа являются «руками» технологии SMT, и, притом, очень быстрыми и хирургически точными: современное монтажное оборудование способно с высочайшей производительностью и степенью точности оборудовать печатные платы элементами, которые остаётся лишь припаять для получения готового устройства.
В статье мы рассказали о технологии SMT и о самих компонентах (SMD), а об особенностях и конструкции оборудования, познакомили вас с несколькими моделями современных SMT-станков.