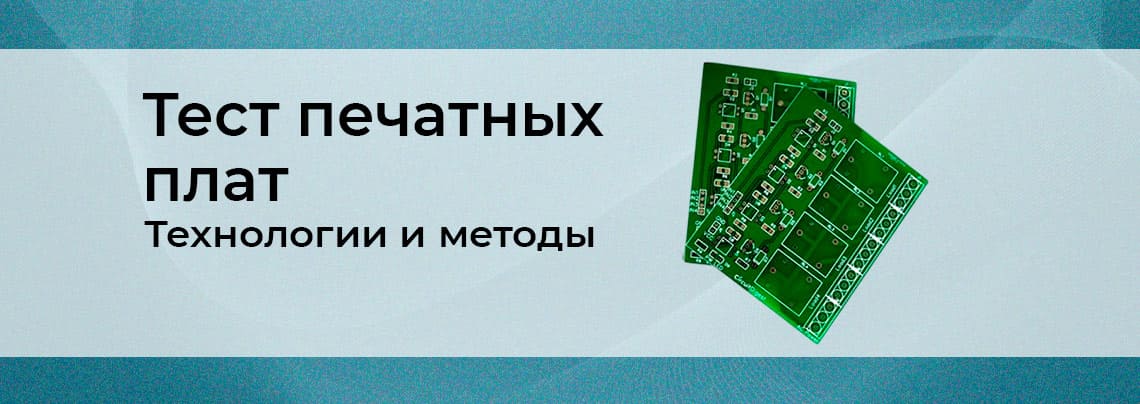
Всем нам хорошо знакомо понятие «брак». Я не о союзе мужчины с женщиной, а о том, с чем борются производители разной техники. Брак — некачественная продукция, недостатки которой мешают её эксплуатации и вообще реализации потребителю. Это такая же часть производства, как, собственно, выпуск продукции нормального качества. Даже при тщательнейшем соблюдении всех регламентов технологического цикла, никто не гарантирует 100% выхода товара нужного качества. Конкретных причин, вызывающих производство бракованной продукции, довольно много. А у каждого вида производств они разные.
Производство электронной техники тоже не лишено недостатков. Даже чрезвычайно автоматизированный и контролируемый на всех этапах процесс иногда приводит к производству дефектной аппаратуры. Причинами могут быть, для примера, применение неисправных комплектующих, входной контроль которых невозможен или связан с трудностями (как правило, экономическими), образование дефектов при монтаже (размещения и/или пайки) электронных компонентов (статья «Несколько слов об оборудовании для монтажа SMD компонентов»), а также неисправность печатной платы (статья «Проектируем печатную плату. Часть 1»). Об этом мы сегодня поговорим.
Время чтения: 28 минут
Тестирование печатных плат? Это очень просто!
Несколько слов о печатных платах
Тестирование стало предметом пристального внимания только в конце 1950-х годов, когда производство массовой продукции резко переключилось с навесного монтажа на поверхностный (статья «Проектируем печатную плату. Часть 2»). Модели того времени по современным меркам крайне примитивны, имеют очень разреженную компоновку, а комплектуются крупными выводными компонентами. Тогда их проверяли вручную простыми контрольно-измерительными приборами.
Сложность современных плат, обусловленная их многослойностью, порождающей множество скрытых печатных проводников во внутренних слоях, чрезвычайная плотность компоновки с высокой степенью миниатюризации электронных компонентов создают широкое поле проблематики их тестирования, которое всегда должно выполняться. Применение микрополосковых волноводов и антенн на них также требует особых методов проверки, причём обязательно (статья «Проектируем печатную плату. Часть 3»). А это — единственная гарантия качества, надёжности, экономии.
Печатная плата (ПП, Printed Wiring Board (PWB), Printed Circuit Board (PCB)) предусматривает как механическое крепление электронных компонентов, так и их электрическое соединение. Иногда она также служит для отвода тепла рассеиваемой мощности от компонентов.
Современные ПП, применяемые в массовом производстве, в основном изготавливаются из фольгированного медной фольгой стеклотекстолита марки FR-4. Базовый материал FR-4 — композит из множества слоёв стеклоткани, соединённых воедино с помощью синтетических эпоксидных смол. Его особенности значительно влияют на свойства и качество конечного продукта, поэтому приходится тщательно его подбирать. Помимо стеклотекстолита, базой выступает керамика (для высокочастотных схем), алюминий (для теплонагруженных узлов), полиамид (для гибких плат), некоторые другие материалы. ПП содержит от 1 до 32 слоёв меди.
Помимо высокой степени уплотнения с миниатюризацией, производство современных ПП связано с повышением экологической безопасности готовых изделий в общем, а в частности — с отказом от применения свинецсодержащих при переходе на бессвинцовые (Pb-free) припои. Директива Европейского союза, ограничивающая содержание вредных веществ RoHS, помимо запрета на использование свинца, также ограничивает применение ртути, кадмия, шестивалентного хрома, других токсичных материалов.
Но использование бессвинцовых припоев — причина множества негативных моментов при производстве PWB:
- Компоненты. Пайка бессвинцовыми припоями требует повышения температуры примерно на 50–70°C. Многие компоненты, особо чувствительные к температуре, ещё проще перегреть. Поэтому в продаже есть специально разработанные версии для пайки именно бессвинцовыми припоями. Обычные компоненты могут не выдержать повышенной температуры: возможно нарушение функциональности и/или образование трещин в корпусе. Пластиковые корпуса имеют тенденцию впитывать влагу из атмосферы, а повышенная температура пайки приводит к скоротечному её испарению с образованием дефектов. Пайка бессвинцовыми припоями требует организации правильного хранения компонентов в условиях пониженной влажности.
- Пайка волной. Переход на бессвинцовые припои внёс множество трудностей в классический поточный монтаж: так называемую пайку волной. Повышенная температура паяльной ванны увеличивают скорость образования твёрдых нерастворимых оксидов элементов, входящих в состав припоя, что проявляется в виде различных дефектов (каверн, разрывов или, наоборот, мостиков и т. д.).
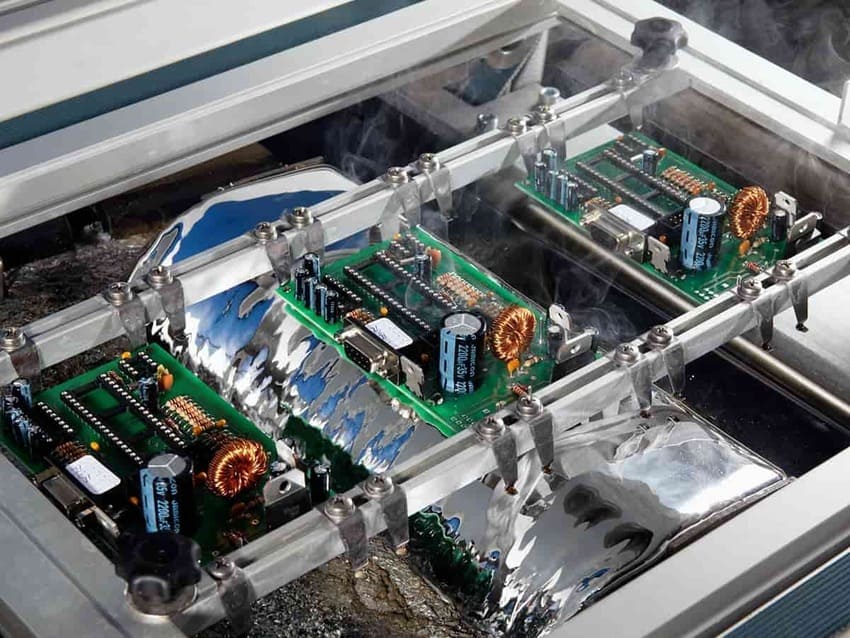
- Окисление. Большинство припоев без содержания свинца (Pb) состоят из сплава олова (Sn), меди (Cu), серебра (Ag), индия (In), цинка (Zn), висмута (Bi) или сурьмы (Sb). Сплав «олово-серебро-медь» (SnAgCu) часто применяют в качестве замены классического припоя «олово-свинец» (SnPb). К сожалению, серебро, висмут, медь и цинк быстро окисляются, тем самым ухудшая смачивание припоем контактных площадок и выводов компонентов в процессе пайки. Для предотвращения окисления необходимо применение инертной среды — азота в рабочей зоне, что усложняет, а ещё удорожает процесс пайки волной.
- Тестирование. Более высокие температуры приводят к ещё большему количеству остатков флюса на контактных площадках и выводах компонентов. Это не даёт надёжного электрического контакта при тестировании методом зондирования. Требуется принятие дополнительных мер для его надёжности.
- Печатные платы. При пайке бессвинцовыми припоями ПП подвергаются воздействию повышенных температур, что приводит к ещё большим температурным деформациям, которые становятся серьёзной проблемой надёжности готового изделия. Также увеличивается вероятность расслоения структуры и отрыва печатных проводников от основного слоя.
- «Усы» и «оловянная чума». «Усы» — нитевидные структуры, которые развиваются и растут на чистых лужёных металлических поверхностях. Они способны вызывать короткие замыкания между двумя соседними проводниками или сбои при прохождении сигнала на высоких частотах. «Усы» стали очевидной проблемой только после перехода на производство электроники без использования свинца, что заставило применять особые составы припоев. «Оловянная чума» — известный ещё с древности процесс разрушения некоторых аллотропных модификаций олова («серое олово»), а также «заражение» устойчивых к разрушению («белое олово»). Разрушающим триггером становятся низкие температуры, ионизирующее излучение и другие. «Оловянная чума» наиболее характерно проявляется у чистого олова или сплавов с высоким его содержанием.
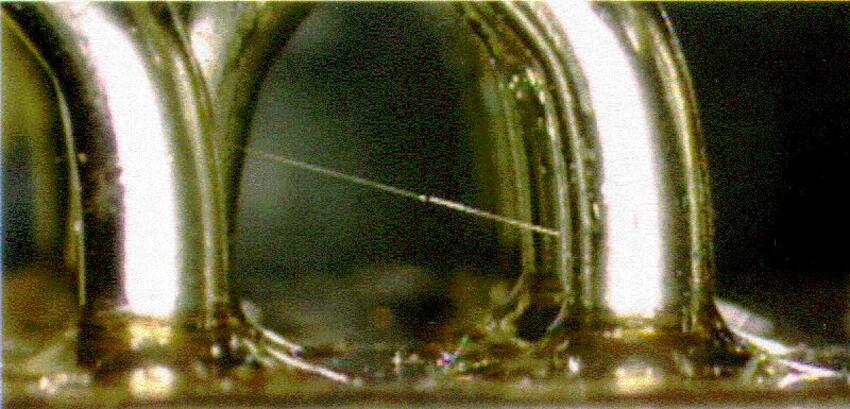
Все эти негативные моменты перехода на бессвинцовую технологию пайки стали ещё одним фактором для обязательности выходной диагностики ПП после монтажа компонентов.
Зачем нужно тестирование
Диагностирование электроники — это один из этапов производства, который призван поддерживать качество, экономичность и надёжность на высоком уровне. Оно заключается в обнаружении непреднамеренных схемотехнических и функциональных различий между произведённым устройством и его предполагаемой конструкцией. Такие различия называются дефектами. Обнаруживая его, мы гарантируем, что только годные экземпляры продукции, соответствующие проектным спецификациям, будут отправлены заказчику. Исследуя дефекты, мы разрабатываем, потом корректируем технологический процесс, избегаем их повторного создания, повышая качество производимой продукции.
В современной электронной промышленности тестирование играет важнейшую роль при выпуске и реализации продукта. Важно заметить, что усилия, прилагаемые к нему, различные по степени ответственности и требуемой надёжности конечного продукта. К примеру, бытовая электроника не проходит тех же испытаний, что авионика или аппаратура военного назначения, которые разрабатываются для критически важных с точки зрения ответственности и надёжности применений. Электроника медицинского характера тоже проходит широкий спектр тестов, направленных прежде всего на безопасность применения.
Для бытовой электроники качество — главная цель, которая ограничивается требуемой конечной полнофункциональностью продукта, соответствующей предполагаемому значению. Другими словами, бытовое устройство после производства должно быть полностью исправным. Но электроника для критически важных с точки зрения безопасности применения обязана быть как качественной (полнофункциональной), так и надёжной (безотказной). Тогда устройство в целом, отдельные его компоненты, к примеру, печатная плата, должны проходить серию испытаний в различных «экстремальных» условиях.
В целом, роль тестирования заключается как в повышении качества, так и в экономии, которые жёстко взаимосвязаны. Качество определяет лояльность или удовлетворённость клиента, а экономия определяет экономические показатели. Определение степени надёжности электронного устройства — ещё одна важная роль тестирования. Надёжность напрямую связана с экономией, поскольку, когда продукт длительное время без нареканий эксплуатируется на стороне клиента, компания экономит на расходах гарантийного обслуживания, сохраняет хорошую репутацию, что, на самом деле, «дорогого стоит».
Тестирование ПП — затратный процесс, отнимающий относительно много времени. Хотя он преизобилует тонкостями и сложностями, почти всегда мотивируется требованиями к высокой надёжности (когда «деньги значения не имеют»), а ещё — экономией (когда деньги значения как раз-таки имеют). Тесты требуют инвестиций в оборудование, производственные циклы, инженерно-технический персонал. В зависимости от требований к конечному продукту, производят контроль только электрических соединений в укомплектованной электронными компонентами ПП или комплексно тестируют все её параметры, включая физические и электрические характеристики базового материала и т. д.
Проверка определённо жизненно важно для ответственной с точки зрения безопасности электроники, такой как медицинская, автомобильная, аэрокосмическая, где ценой неисправности будут человеческие жертвы. Такие сферы применяют многократный контроль: от оценки параметров материалов, когда он ещё находится в виде огромных листов-заготовок, до финального входного контроля перед вводом в эксплуатацию.
Экономия — ещё одна причина для производственников. Всем предприятиям электронной промышленности хорошо известно «Правило «десяти», которое означает, что обнаружение дефекта на следующем этапе производства обойдётся в 10 раз дороже, чем на предыдущем. Дефекты на ПП устранить значительно дешевле, если они обнаруживаются как можно раньше. На рисунке ниже показано увеличение затрат на диагностирование в зависимости от этапов производства. В качестве примера рассмотрим неисправную плату, которая не была протестирована. После того как на неё запаяли компоненты, и, если неисправность обнаружили после процесса пайки, ремонт обойдётся дороже, чем на уровне «голой» платы. Как правило, компоненты не могут быть демонтированы и установлены повторно. Таким образом, не обнаруженный вовремя дефект «голой» ПП приведёт к утилизации как её, так и множества электронных компонентов, где многие — очень недешевы.
Неисправность, обнаружившаяся только у конечного пользователя, приводит к тому, что производитель с поставщиком несут высокие расходы на гарантийное обслуживание, а также издержки, связанные со снижением репутации бренда. Тем самым нанося вред бизнесу, побуждая клиента перейти к конкуренту. Подытоживая, можно смело заявить, что чем раньше будет обнаружена неисправность, тем дешевле будет её исправление. Поэтому тестирование как этап раннего обнаружения дефектов устройства решает почти всё.
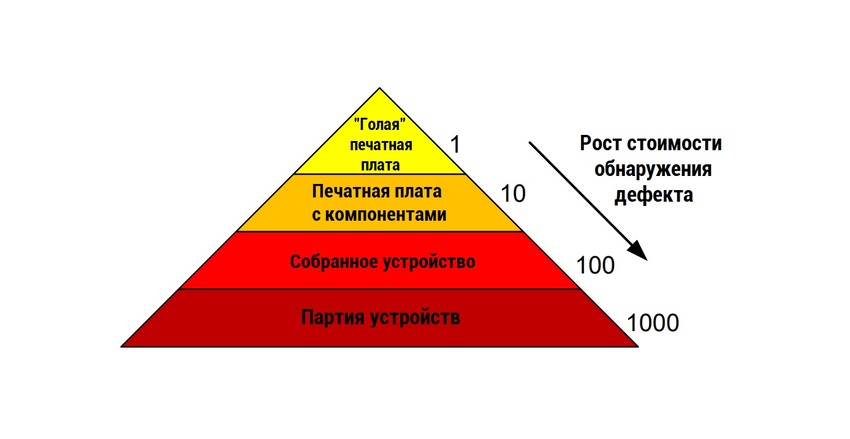
История и перспективы тестирования
Тесты проводили всегда: со времён эпохи электронных вакуумных ламп. Однако тестирование электроники начало развиваться только после изобретения транзистора и массового внедрения печатных плат, что привело к разработке нескольких методов и технологий проверки, когда монтаж становился всё плотнее, а компоненты — миниатюрнее. Появление плат с высокоплотными межсоединениями (High-Density Interconnect, HDI) со встроенными пассивными элементами стало прекрасной возможностью для развития инноваций в области тестирования.
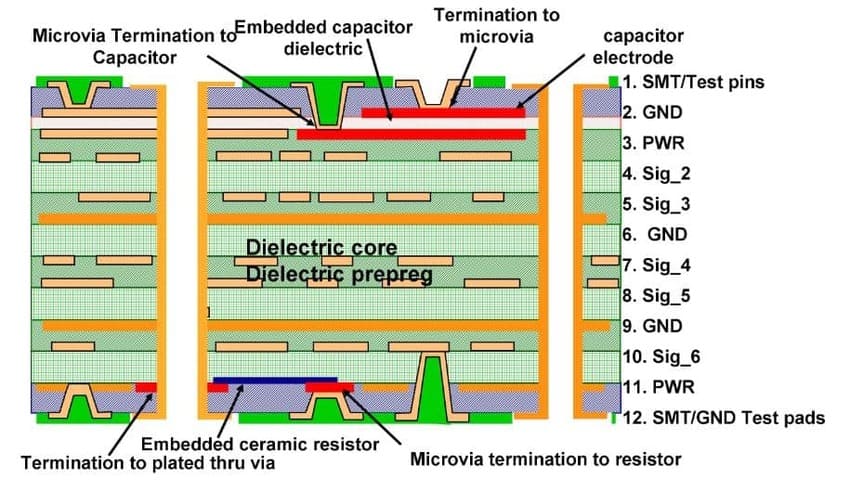
До разработки транзистора (статья «Транзисторы: принцип работы, схема включения, чем отличаются биполярные и полевые») электронные компоненты, такие как резисторы (статья «Как проверить резистор мультиметром?»), конденсаторы (статья «Как выбрать конденсатор?»), электронные вакуумные лампы и другие располагались на ПП довольно разреженно. В то время для качества не требовалось тщательных тестов; скорее, хватало быстрого осмотра с проверкой нескольких соединений. Окончательное подтверждение исправности осуществлялось после окончательной сборки устройства. Такой подход, в общем-то, всех устраивал. После середины 1950-х годов печатные платы стали более сложными, плотными из-за развития транзисторной и интегральной технологии (статья «Что такое полупроводник?»), которая пришла на замену электровакуумным лампам. Параллельно началось освоение цифровой электроники. При большей плотности платы и более объёмных тиражей выпуска обычные подходы к тестированию, которые применялись ранее, больше не были достаточными для определения качества современной (на то время) ПП.
Цифровые устройства дали возможность функционально тестировать ПП перед их интеграцией в системы, используя имеющиеся цифровые входы/выходы для подачи входных сигналов и наблюдения за выходными, а затем сравнивая поведение «испытуемого» с её ожидаемой конечной функциональностью. Этот подход привёл к разработке универсального автоматического испытательного оборудования (Automatic Test Equipment, ATE) для цифровых систем. Оно генерирует тестовые паттерны для тестируемого устройства (Device Under Test, DUT), затем сравнивает ответы с ожидаемыми. После сравнения выдаёт результат тестирования.
Но аналоговые устройства не могли быть проверены так же относительно просто, как цифровые. Разработка подхода к измерениям на основе операционных усилителей (статья «Что такое операционный усилитель?») позволила тестировать отдельные аналоговые компоненты методом зондирования, что стало рождением внутрисхемного тестирования (In-Circuit Testing, ICT) к концу 1960-х годов.
Из-за увеличения сложности ПП функциональное тестирование оказалось очень дорогим и, в некоторых случаях, не покрывающим весь возможный спектр неисправностей. К середине 1970-х годов был разработан подход внутрисхемного тестирования для цифровых схем, который позволял с высокой точностью выявлять в них неисправности (вплоть до конкретного электронного компонента). Подобно аналоговым, для цифровых также стало возможным зондирование и внутрисхемное тестирование как отдельных узлов, так и всего устройства в целом. После этого внутрисхемное тестирование охватывало большинство неисправностей, за исключением проблем из-за физической конструкции платы: задержек распространения сигнала, которые, как и некоторые другие дефекты, можно обнаружить только с помощью функционального тестирования.
По мере развития технологий внутрисхемное тестирование также столкнулось со сложностями. В 1970–1980-х годах корпус Dual In-Line (DIL, он же DIP) был доминирующим среди корпусов интегральных схем. Это время было «золотым» для внутрисхемного тестирования, который требует физического доступа ко всем выводам компонентов. С появлением технологии поверхностного монтажа (SMT) в конце 1980-х годов тестировщикам стало сложно получить физический доступ к выводам компонентов. Миниатюризация SMD стала предпосылкой для появления печатных плат высокой плотности, а это привело к тому, что прямое зондирование выводов стало сложным и дорогим, а компонентов в корпусах BGA в принципе невозможным. При сегодняшнем количестве контактов, достигшем нескольких тысяч с шагом 50 микрон, невозможно для каждого входа/выхода разместить дополнительную контрольную точку.
Тестирование ПП и уж тем более физических и электрических свойств базового материала было несущественным до середины 1950-х годов; то есть до момента появления первого полупроводникового цифрового компьютера компании IBM. В то время какие-то тесты не занимали умы производителей. По мере того как технология развивалась в сторону высокоплотной электроники, миниатюризации корпусов компонентов и повышения рабочих частот, эта традиция изменилась. Особенно с появлением HDI-плат, которые требовали высочайшего качества базового материала и многократного тестирования на всех этапах производства. По статистике неисправные «голые» платы составляют примерно 5% от общего числа односторонних версий, от 5 до 10% от общего числа многослойных и от 10 до почти 100% в моделях с высокоплотными межсоединениями. Более точная геометрия и хрупкость создавали дополнительные сложности в применении ставших классическими методов контроля с помощью зондирования. Для преодоления ограничений, связанных с высокой степенью миниатюризации компонентов и множества слоёв в ПП, были предложены другие более прогрессивные методы проверок, которые, к сожалению, непростые, а их эффективность далеко не 100%.
Помимо ограничений физического доступа к выводам, миниатюризация сделала необходимой оценку характеристического импеданса (волнового сопротивления) печатных проводников, передающих сигналы высокой частоты. Несовершенный процесс травления приводил к отклонениям характеристического импеданса, которые часто недопустимы. В некоторых случаях он специально многократно тестируется для проверки стабильности производства ПП.
Сейчас производство электроники движется в сторону уплотнения, миниатюризации и экологической безопасности. Печатные платы ближайшего будущего, скорее всего, будут иметь встроенные внутрь пассивные и активные компоненты, которые ещё больше затруднят дальнейшее тестирование, полностью ограничив физический доступ. Иногда существующая методология не даёт стопроцентного покрытия всего поля возможных неисправностей и, таким образом, повлияет на скорость поставки продукции и её стоимость. Эта ситуация требует особых инженерных изысканий в области бесконтактного и косвенного тестирования, чтобы улучшить возможную ситуацию. Рисунок ниже показывает хронологию методов и технологий проверок электронной продукции в общем и ПП в частности.
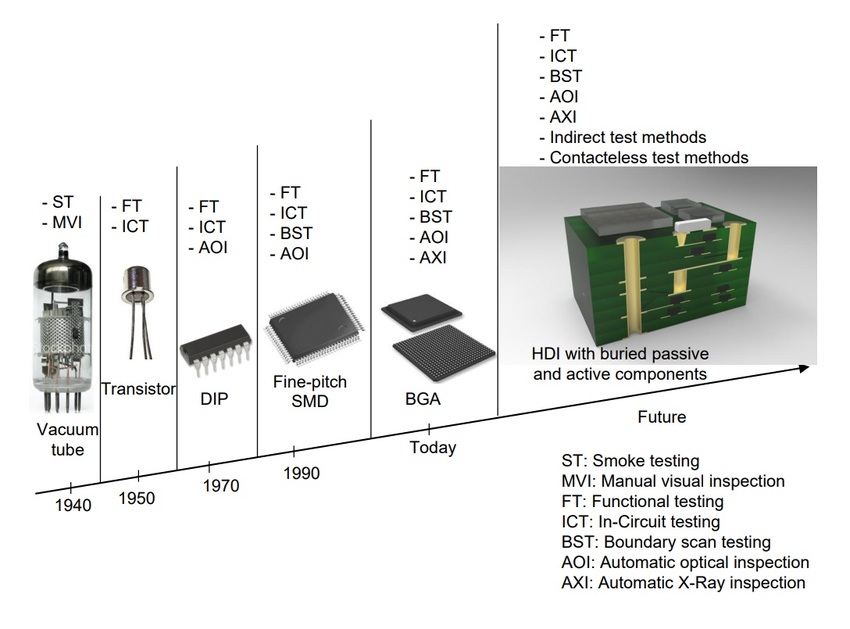
Спектр неисправностей
Дефект на печатной плате возникает на разных этапах производственного процесса. Например, при нанесении паяльной пасты из-за неправильного её количества, при позиционировании компонента машиной для автоматизированного монтажа, при котором он подбирается или размещается неправильно, при неправильном температурном профиле оплавления припоя, что приводит к разрывам, коротким замыканиям и ненадёжной пайке.
Все эти факторы катастрофическому снижают надёжность или веду к полному отказу. Кроме озвученных дефектов, встречаются нарушения самого материала ПП. На рисунке ниже показан полный спектр основных её дефектов и хронология этапов технологического цикла изготовления и сборки (снизу вверх). Сообщается, что обрывы доминируют в спектре, составляя около 41% от общего числа дефектов в современных моделях. За ними следуют короткие замыкания или мосты, которые соответствуют 20% от общего числа проблем.
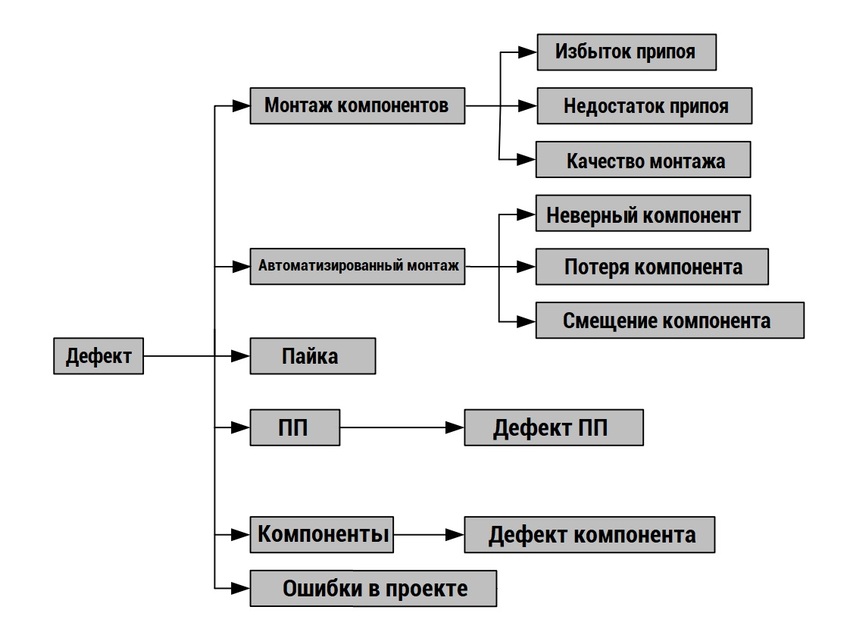
Обрыв
Это как требуемого должного электрического контакта двух точек или разрыв проводника в этой цепи. Этот тип дефекта критически, поскольку приводит к немедленному отказу схемы. Основные причины его появления связаны со следующим:
- Паяльная паста. Когда она забивается в отверстия трафарета и не попадает на контактную площадку или нанесена в недостаточном количестве, то происходит непропайка соединения. Тогда надёжного электрического контакта в этом месте не будет.
- Процесс пайки. Неправильная настройка температурного профиля печи оплавления припоя приводит к неполному расплавлению шариков, тем самым создавая обрывы в местах, где должно быть соединение.
- Автоматизированный монтаж компонентов. Сбои в работе машин для автоматического монтажа приводят к отсутствию компонента там, где он должен быть, и, соответственно, образованию обрыва.
- Эффект «надгробного камня». Низкое качество припоя, загрязнение контактных площадок или их неправильный размер, температурные неравномерности в зоне пайки являются основной его причиной.
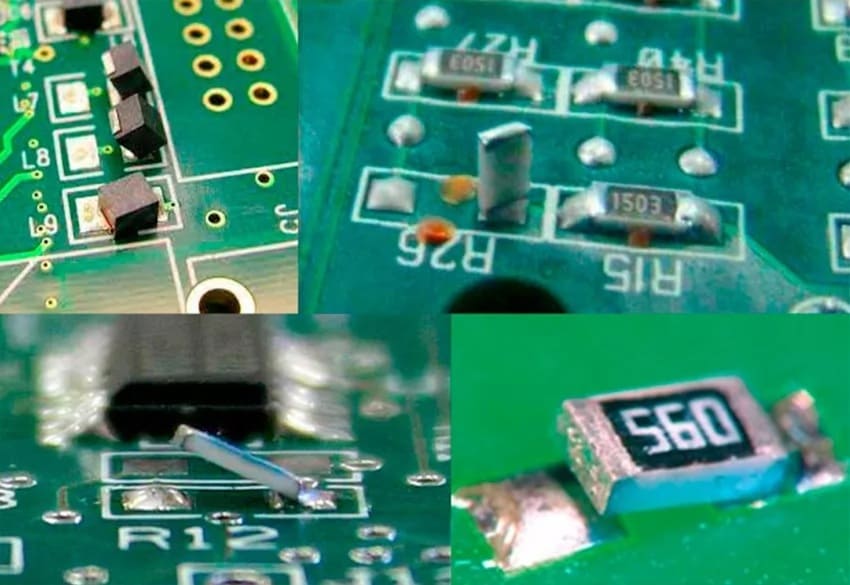
Короткое замыкание или мост
Он определяется как наличие припоя между двумя точками платы, которые не должны иметь электрического контакта между собой. Мосты, как и обрывы, также важны, поскольку они приводят к немедленному отказу устройства. Есть несколько факторов, которые вызывают их образование. Обычно мосты возникают по следующим причинам:
- Ошибка позиционирования трафарета. Как правило, это приводит к образованию множества мостов одновременно.
- Избыток паяльной пасты. Обычно возникает из-за неверного дозирования или слишком большого отверстия в трафарете или маленького размера контактной площадки.
- Паяльная паста. Мосты также образуются, когда соотношение олова и других металлов и флюса в составе паяльной пасты неверно. В этом случае металлические компоненты пасты оседают и растекается.
- Температурный профиль оплавления припоя. Неправильный термопрофиль тоже приводит к образованию мостов.
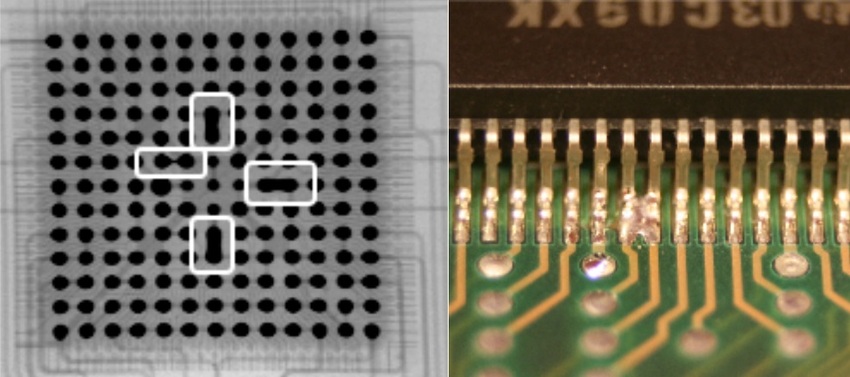
Дефекты, вызванные применением бессвинцового припоя
Из-за директивы об ограничении использования опасных веществ (RoHS) промышленность перешла на бессвинцовые способы монтажа. Этот переход существенно повлиял на электронную промышленность во многих отношениях. Одним из последствий стала увеличившаяся температура оплавления. Воздействие на некоторые компоненты повышенных температур приводит к деформации и повреждению. Вот компоненты, которые наиболее чувствительны к перегреву:
- Алюминиевые электролитические конденсаторы.
- Керамические SMD-конденсаторы.
- Разъёмы.
- Радиочастотные и оптоэлектронные компоненты.
Помимо непосредственного ущерба, переход на бессвинцовую электронику плохо повлиял на надёжность соединений в условиях высоких температур с вибрациями.
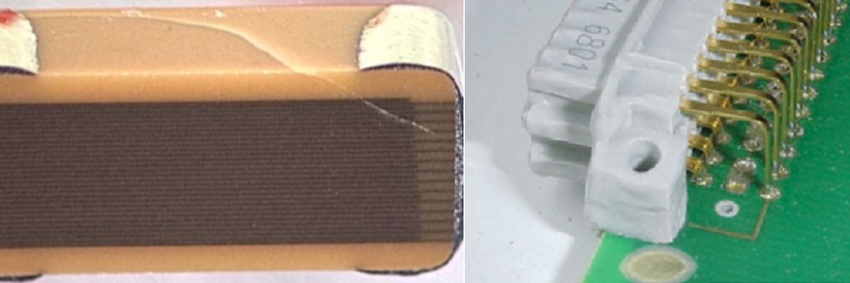
Дефекты травления печатных плат
После травления лишней меди нельзя игнорировать предположение о том, что некоторые платы потом становятся неисправны, поскольку могут возникнуть несколько типов дефектов. Например, обрывы печатных проводников (перетравление) и мосты (недотравление), которые будут означать стопроцентную неисправность. Другие типы дефектов, такие как «мышиные укусы», «шпоры», утончённые дорожки, иногда не столь существенны для сигналов постоянного тока, как обрывы или мосты, но критически для радиочастот, так как вызывают перекрёстные помехи и несоответствие характеристического импеданса.
Степень серьёзности этих типов дефектов зависит от частоты аналоговых сигналов или от тактовой частоты при прохождении по ним цифровых. Более того, эти дефекты создают проблемы в высоковольтных устройствах, снижая напряжение пробоя между дорожками. Большинство из них выявляются визуальным или оптическими методами контроля. На рисунке ниже схематически показаны дорожки так, как они были спроектированы на компьютере, а также реальные, получившиеся после травления, а также список типичных дефектов ПП.
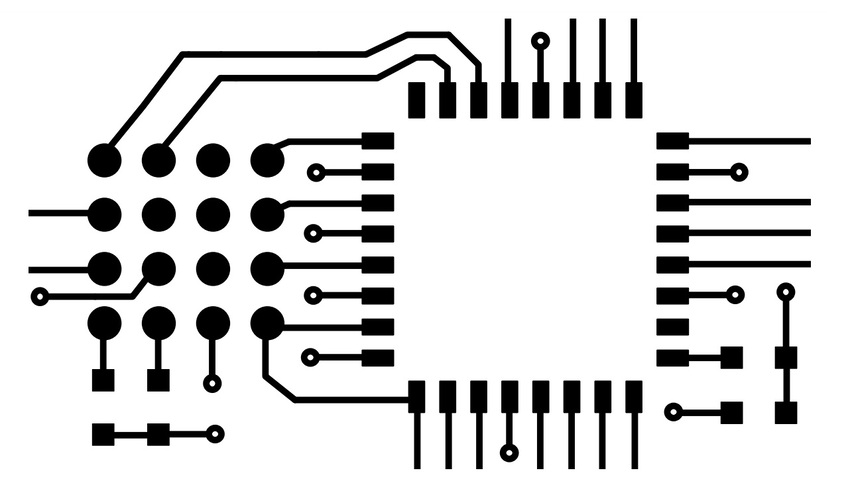
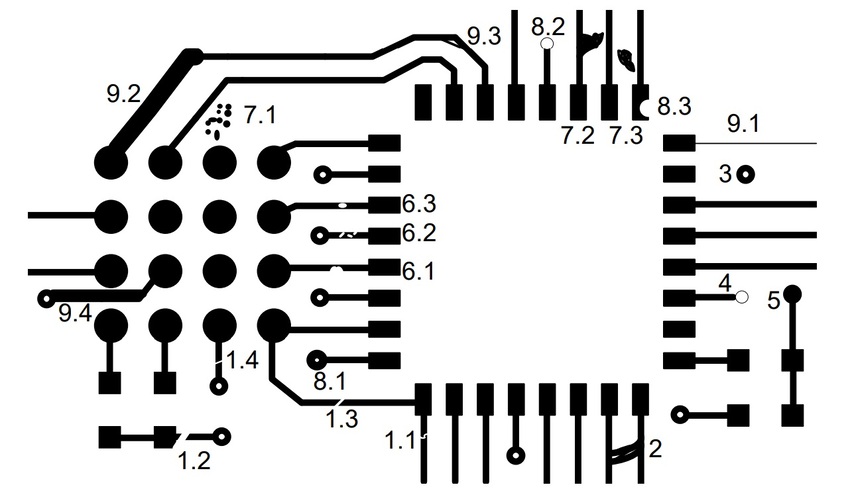
Дефекты, влияющие на прохождения сигналов постоянного тока
1. Обрыв | 2. Короткое замыкание или мост | 3. Отсутствие дорожки | 4. Ошибка проектирования | 5. Отсутствие переходного отверстия |
1.1 Перелом | - | - | - | - |
1.2 Порез | ||||
1.3 Царапина | ||||
1.4 Трещина |
Дефекты, влияющие на прохождения высокочастотных сигналов
6. Частичная проводимость | 7. Паразитные элементы рядом с волноводом | 8. Нарушение конфигурации контактной площадки | 9. Изменение в геометрии волноводов |
6.1 «Мышиный укус» | 7.1 «Пятна» | 8.1 Недотравление | 9.1 Утончение |
6.2 Зазубрины | 7.2 «Шпоры» | 8.2 Перетравление | 9.2 Уширение |
6.3 Прокол | 7.3 «Мазки» | 8.3 Обрыв | 9.3 Дублирование |
9.4 Флуктуация ширины |
Характеристический импеданс
Его несоответствие заметно влияет на целостность сигнала, потерю мощности при передаче радиочастотных и высокоскоростных сигналов между парой «источник-приёмник». Оно вызывает множественные переотражения сигнала вперёд-назад между устройствами и, следовательно, всплески с провалами, что приводит к ошибкам при передаче.
Проверка корректности характеристического импеданса для печатных дорожек по передаче высокоскоростных и радиочастотных сигналов, необходимо. После производственного процесса он выходит за пределы ожидаемого диапазона из-за нарушений в технологическом процессе выпуска платы и допусков на составные материалы.
Характеристическое сопротивление дорожки определяется несколькими факторами, включая ширину w; толщину дорожки t; толщину h; относительную диэлектрическую проницаемость изолятора εr. Кроме того, геометрия профиля сечения дорожки также является ещё одним фактором, который влияет на характеристическое сопротивление. В зависимости от типа травления дорожка имеет несколько профилей сечения.
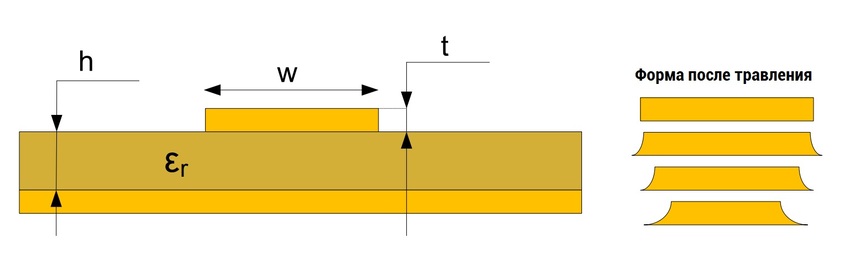
Ввиду особенностей базового материала ПП дорожки в ней лежат на неоднородном диэлектрике, где некоторые находятся на верхней части подложки, где преобладает эпоксидная смола, а другие — на верхней части подложки, где больше стеклянного волокна. Это явление вызывает изменения характеристического сопротивления между дорожками даже в пределах одной ПП.
Читайте продолжение статьи во второй части !
Желательным способом минимизации брака от некачественных печатных плат ещё до их серийного изготовления или заказа является всестороннее тестирование множества образцов от всех возможных поставщиков. В процессе этого тестирования следует выявить качество базового материала, стабильность выходных характеристик готовой продукции. Такой подход позволит сократить финансовые издержки при дальнейших этапах тестирования. Сегодня вы узнали про частые проблемы при монтаже, а вот как правильно протестировать платы — читайте во второй части статьи.